What is the ratio of Bar to ingot for forging?
At our shop something that is subsequently forged must be made from bar with a minimum 5:1 reduction ratio from the original ingot, bloom, or billet. If the product is to be machined directly from bar with no subsequent working we require 10:1.
What is a stock for forging?
(2) A piece of stock for forging that is cut from bar or billet lengths to provide the exact amount of material needed for a single workpiece. Natural draft — Taper on the sides of a forging, due to its shape or position in the die, that makes added draft unnecessary.
How to get a forged steel bar?
Most steel mills will be specific that their product is a "rolled bar". You will probably need to find an open die forging operation to obtain a forged bar. You can google Scot Forge for a start. It boils down to reduction ratio for end product use by your client. It may also depend upon the grade of steel in question.
What is the difference between forging and rolling bars?
With a rolled bar, the ingot or bloom is brought to size by passing it through two rolls, often several sets of rolls. In general, forging produces more hot work through the thickness of the bar that rolling will. At least, many will believe it does.
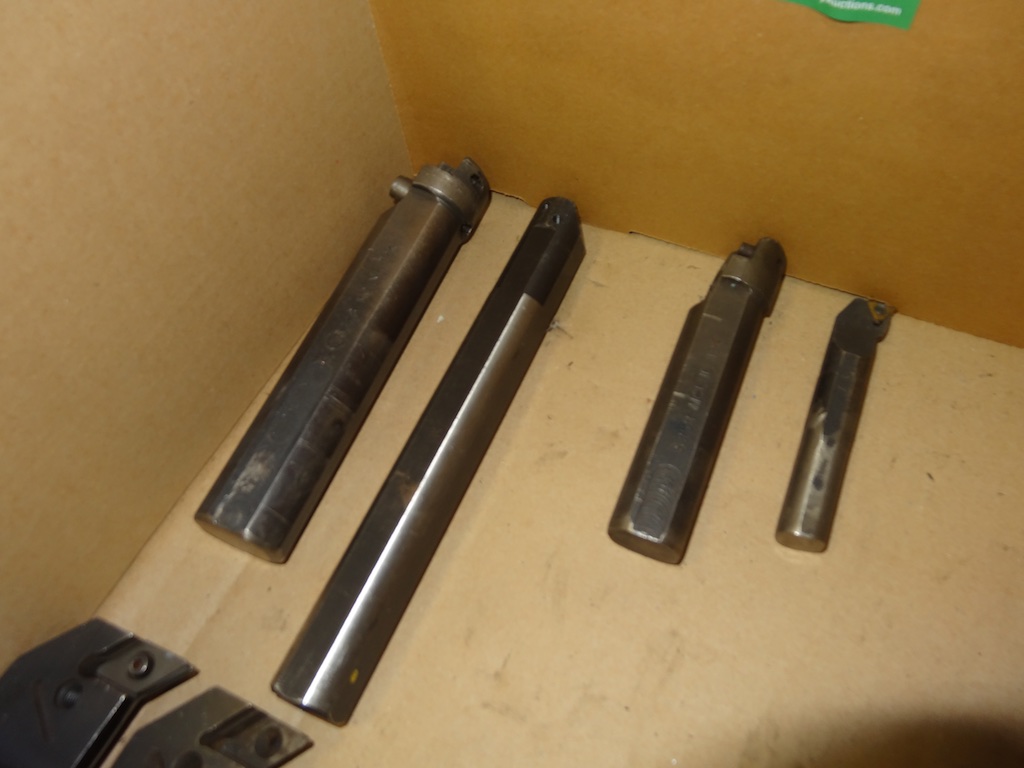
What is the scale when forging?
Hammerscale, also written hammer scale, is a flaky or spheroidal byproduct of the iron forging process (for modern equivalent, see mill scale). Hammerscale is almost universally recovered from archaeological excavations in areas where iron ore was refined and forged.
Are forged knives better than stock removal?
Most would agree the primary difference is the amount of strength that forging retains out of the steel. This is because the milling process creates a “grain” in which the metal is structured. Stock removal keeps this grain uniform regardless of shape, which lends it a slightly weaker strength.
How do you spread metal forging?
0:577:28Beginner Blacksmithing how to spread metal - YouTubeYouTubeStart of suggested clipEnd of suggested clipYou got to hold the punch and the hammer which means you've got to use the blacksmith's. Third handMoreYou got to hold the punch and the hammer which means you've got to use the blacksmith's. Third hand to hold the metal. Um so just put the punch on there giving it a couple knockdowns.
Does forging steel make it stronger?
Forged steel is generally stronger and more reliable than castings and plate steel due to the fact that the grain flows of the steel are altered, conforming to the shape of the part. The advantages of forging include: Generally tougher than alternatives.
Can I forge stainless steel?
Stainless steel is one of the best types of steel for forging. This is because stainless steel reacts very well in the forging process. Its best qualities, particularly its strength and corrosion resistance, are enhanced by the forging process. Additionally, forging creates a continuous grain flow throughout the part.
Does forging a knife make it stronger?
No, “forged”/smithed knives are not stronger, sharper, or in any shape or form better than knives made using the stock removal method. As a matter of fact, custom knives in general are not stronger, sharper, or in any shape or form better than knives made using the stock removal method.
What do they sprinkle on steel when forging?
Devoid of oxygen, the metal forms a layer of iron-oxide called wustite on its surface. When the metal is hot enough, but below the welding temperature, the smith sprinkles some sand onto the metal. The silicon in the sand reacts with the wustite to form fayalite, which melts just below the welding temperature.
How hot is a blacksmith forge?
3,000 to 4,000 degrees FahrenheitBlacksmiths cook the coal until most of the impurities are burned off. The result is coke, a fuel that is almost entirely carbon allowing us to reach temperature of 3,000 to 4,000 degrees Fahrenheit at the core of the fire! Fire this hot can quickly get the metal up to welding temperatures at about 2,500 degrees.
How much do blacksmiths make?
Salary Ranges for Blacksmiths The salaries of Blacksmiths in the US range from $22,060 to $63,560 , with a median salary of $37,730 . The middle 60% of Blacksmiths makes $37,730, with the top 80% making $63,560.
Does forging reduce grain size?
This grain size can be changed significantly by further heat treatment or forging operations, and it is important to understand what controls these changes.
Does forging increase hardness?
The high-temperature manual forging process increases the hardness of knives of each material. In fact, the hardness level increased after different treatments.
Is steel harder to forge than iron?
Steel is stronger than iron (yield and ultimate tensile strength) and tougher than many types of iron as well (often measured as fracture toughness).
Which forging process controls the ring height?
The axial roll s control the ring height during the rolling process. Axisymmetric forging — A forging where metal flow, during deformation, is predominately in a direction away from a common axis in a radial direction. Backward extrusion — Forcing metal to flow in a direction opposite to the motion of a punch or die.
What is block forging?
Block — The forging operation in which metal is progressively formed to general desired shape and contour by means of an impression die (used when only one block operation is scheduled).
What is block first second finish?
Block, first, second, and finish — The forging operation in which the part to be forged is passed in progressive order through three tools mounted in one forging machine; only one heat is involved for all three operations.
How many blocks are needed for a forging?
As many as three blocker dies are sometimes needed for some forgings and up to three operations are sometimes required in each die.
How does grain flow improve forging?
Grain flow produced by proper die design can improves the mechanical properties of forgings. Grain growth — An increase in the size of the grains of a metal with a proportional reduction of the number of grains. Grain separation — In forging aluminum, rapid metal flow sometimes causes a separation or rupture of grain.
What is a bar in a form?
Bar — A section hot rolled from a billet to a form, such as round, hexagonal, octagonal, square, or rectangular, with sharp or rounded corners or edges, with a cross-sectional area of less than 16 sq in. (A solid section that is long in relation to its cross-sectional dimensions, having a completely symmetrical cross section and whose width or greatest distance between parallel faces is 3/8 in. or more).
How wide is a steel bloom?
For steel, the width of a bloom is not more than twice the thickness , and the cross sectional area is usually not less than about 36 sq. in. No invariable rule prevails for distinguishing between blooms and billets; the terms are frequently used interchangeably.
Why is forging the shape of knives better?
Forging to shape provides a minor change to the orientation of the “grain” but there would still be reduced toughness in the direction where the tip can more easily break. Whether forging or using stock removal it is better to produce knives along the rolling direction instead to make the tips less prone to breaking.
Why do you forge knives?
There are many reasons to forge that aren’t performance-related. Forging close to shape can mean less steel is lost to grinding compared to stock removal. One obvious reason to forge is for producing forge welded Damascus steel. Producing those steels provides another artistic avenue when it comes to knifemaking and the possibilities are nearly endless. On the flip side, there are commercially produced Damascus steels for stock removal makers, though the maker is limited to the Damascus options that are available. Some knives are more feasible to produce when forged, including curved blades or knives with integral bolsters. It is possible to produce those knives with stock removal but there is more material loss. For some customers and makers they like the “rustic” look from having some scale on the unground portion of the blade. That look is easiest to produce by forging. Another reason to forge is for continuing the tradition of producing knives in that way. It is certainly possible to enjoy producing knives with a hot forge, hammer, and anvil. The best reason to forge a knife is because you want to.
What steels are used for forging?
However, the most common steels used for forging: 52100, 1095, 5160, W 1, etc. the carbides are fully dissolved at forging temperatures and grain growth occurs relatively rapidly. CruForgeV and W2 have some vanadium carbide which is stable to higher temperature to help suppress grain growth.
How thick is knife steel?
With knife steel it has typically started with an ingot several inches in thickness (10″ or so) and has been reduced to 1/4″ or thinner. The knifemaker then forges it to shape, sometimes with some reduction in thickness as well.
How is an ingot heated?
The ingot is then heated up to high temperature and forged either with a hammer or press to a form ready for hot rolling. In some cases the ingot is ready for rolling as-produced. Next the steel is hot rolled to the final desired thickness.
What is the ingot size of steel?
A typical ingot size for tool steel or high speed steel might be 10″ thick either round or square depending on the production process and the desired final shape. Smaller ingots are better for limiting the segregation of alloying elements and keeping the cast structure fine. At that point the steel is in “cast” form.
Which is easier to forge: stainless steel or carbon steel?
Stainless vs Carbon Steel. Low alloy steels are easier to forge, as described in this article, and are by far the most commonly used by forging bladesmiths. When it comes to forging to shape, the properties of high alloy steels are more sensitive to direction because of carbide banding.
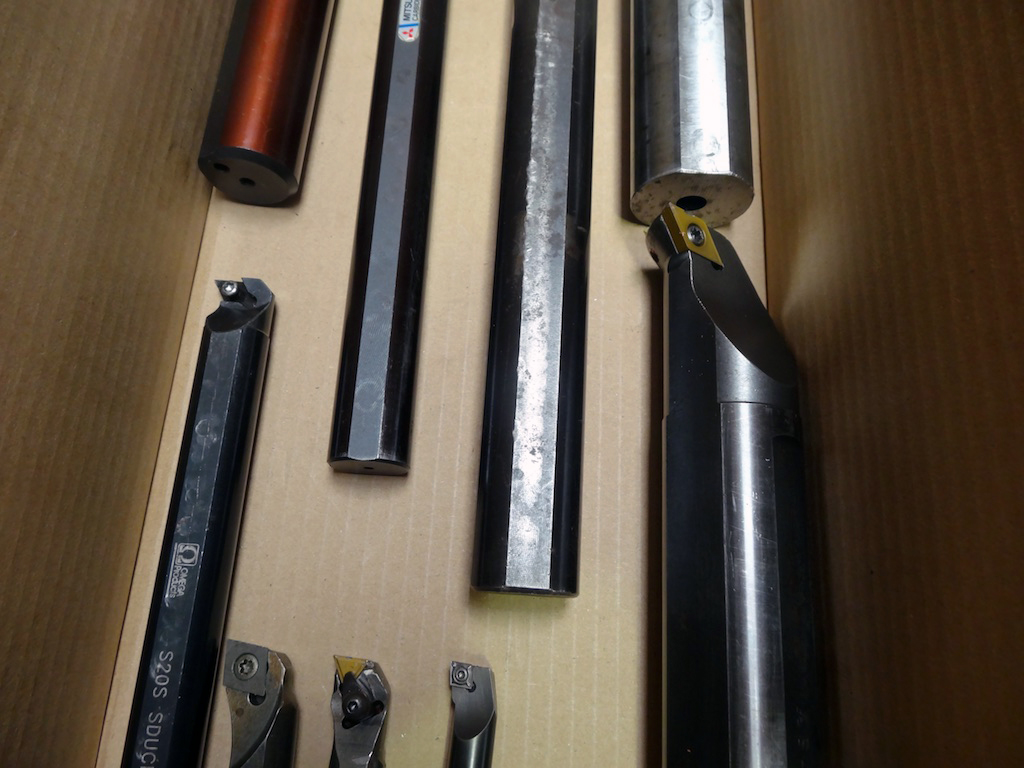