
Full Answer
What are stockouts and how to prevent them?
What causes products to be out of stock?
- Disparities between item counts. One of the most common causes of stockouts is a disparity between item counts or a record of how many units of a particular item a ...
- Inadequate forecasting and inaccurate reporting. Stockouts, and inventory shortages in general, are often caused by unexpected surges in consumer demand.
- Delivery and logistics problems. ...
What does 'stock out' mean?
What is a Stockout? A stockout occurs when customer orders for a product exceed the amount of inventory kept on hand. This situation arises when demand is higher than expected and the amount of normal inventory and safety stock is too low to fill all orders.
Which stock should you buy?
When participants buy new stocks at a discount relative to their expected open market price, they can score a quick profit. Thanks to companies like ClickIPO and Robinhood, which offer pre-IPO access to regular buyers, average Joe investors can also benefit from that sweet pop. Just ask those who took a swing at LegalZoom.
How to calculate stockout risk?
- Blog
- Jan. 26, 2022 Branding your small business in 5 basic steps
- Jan. 19, 2022 8 practical tips for virtual meetings
- Jan. 8, 2022 Big Ideas in sales: A look at what’s next for better sales kickoffs and presentations
- Latest posts

What is meant by stock outs?
A stockout is when inventory becomes unavailable, preventing an item from being purchased or shipped, resulting in a loss in sales. Stockout costs include the loss of income and customers due to a shortage of inventory from a stockout.
What causes a stock out?
Stock-outs are caused by the following, the most significant being listed first: Under-estimating the demand for a product and, therefore, under ordering. Late delivery by a supplier. You ordered enough, but your supplier did not deliver when expected or only delivered part of your order.
Are stock outs good?
Stockouts almost always make it to the “worst nightmare” lists of retailers, and for good reason. Not only do they lead to lost sales, but out-of-stocks also result in reduced customer satisfaction and lower loyalty levels.
What is stock in and stock out?
phrase. If goods are in stock, a shop has them available to sell. If they are out of stock, it does not.
How do you avoid stock out?
How to reduce stock levels and avoid stock outs.Master your lead times.Automate tasks with inventory management software.Calculate reorder points.Use accurate demand forecasting.Try vendor managed inventory.Implement a Just in Time (JIT) inventory system.Use consignment inventory.Make use of safety stock.More items...
What is the effect of stock outs?
The most obvious consequence of stockouts is lost revenue. If a customer goes to place an order and the item is out of stock, you lose the profit of that sale. Shoppers may opt for cheaper products. Or even worse, you may lose a customer forever, which means less recurring sales in the future.
Why is it important to avoid stock out in the market?
Stockouts can lead to lost sales, since customers are more likely to look elsewhere for the necessary items if you don't have them available. This can also have a negative impact on customer satisfaction.
How is stock out cost calculated?
Raw material requirement per day = 2,070,465 / 300 = 6,902 Kg / days. This following are Stock Out Cost (SOC) calculation: • Raw material requirement (2012) = 2,070,465 Kg / 300 days = 6,901 kg / day • Purchase price difference (if forced to buy if shortage) called as shortage cost = IDR. 250.
Why are so many things out of stock?
The highly contagious new COVID-19 variant that's causing record infections in the U.S. is undoubtedly one of the biggest stressors on the food industry right now. Grocery store workers are catching the virus in higher numbers and calling out sick, making it tougher for markets to keep shelves stocked.
What is the general rule regarding stock outs?
To minimize stockout risk, suppliers should focus on augmenting their retail execution and supply chain practices. As a general rule of thumb, companies should aim to eliminate OOS for the 20% of items that account for 80% of total sales to make the greatest impact on the bottom line.
What is the meaning of currently out of stock?
Items that are currently out of stock, also known as a stockout, can be defined as the unavailability of specific items or products at the point of...
How can stockouts be prevented?
Stockouts can be prevented by reconciling disparities in item counts by using a unified inventory management system.
Does out of stock mean discontinued?
No, out of stock simply means the vendor does not currently have the item, but it will become available again once stock is replenished.
What causes a stock out?
One of the most common causes of stockouts is a disparity between item counts or a record of how many units of a particular item a retailer has in...
What are the consequences of stock shortage?
Stock shortage leads to lost sales and lost revenue as customers are unable to purchase the items they want.
What is stock out cost?
Stockouts cost retailers an estimated $1 trillion every year, and shoppers experience stockouts as frequently as every third shopping trip in some...
What is a stockout in retail?
Stockouts can be defined as the unavailability of specific items or products at the point of purchase when the customer is ready to buy. In bricks-and-mortar stores, this usually means obvious gaps in a store’s shelves.
What does it mean when a store is out of stock?
When popular items are out of stock, retailers are literally leaving money on the table and inviting their shoppers to take their business elsewhere.
How do retailers react to stockouts?
Many retailers react to stockouts rather than taking proactive steps to prevent them. But reacting means retailers are constantly on the defensive. With a little planning and the right tools, retailers can proactively avoid out-of-stocks and ensure their customers are happy.
What is it called when a store runs out of stock?
Yet even the most diligent customer-focused stores can still struggle with one of the biggest challenges any retailer can face—running out of stock. Stockouts, also known as out-of-stocks, are among the most frustrating experiences for online and in-store shoppers. Stockouts don’t just create disappointment and frustration for customers.
Why do stockouts occur?
Technical issues. Shrinkage, or the loss of goods due to damage or theft.
What would happen if most retailers had still had the toy in stock?
But if most retailers had still had the toy in stock and one retailer in particular did not because of supply-chain issues or poor inventory management, then that retailer’s product shortage would be considered a stockout.
Why is my inventory out of stock?
Another common reason for an out-of-stock is inadequate or inaccurate inventory forecasting. Anticipating demand for specific products is a major challenge for retailers. Recent data suggests that 73% of retailers struggle with inventory forecasting.
What is a stockout?
Stockout or out-of-stock (OOS) is a condition in which the inventory of a particular product is depleted. For a retail store, stockout is a term for a product that is not available at this store shelf but may be available in another location in the supply chain.
What causes a stockout?
Inefficient supply chains or store operations are the leading causes of stockouts. Here are the 3 most common reasons for the out-of-stock situation.
What are stockout costs?
Stockout costs are the costs for retailers due to out-of-stock items, including the following 4 components:
How stockouts can hurt your business?
Stockout can hurt retailers, their customers, and suppliers. However, the approach to answering this question is from the customer’s point of view.
How to prevent stockouts
Thankfully, you can prevent most of the underlying causes of stockouts with effective retail store operation procedures. You should strengthen your retail activities and practice effective supply chains to minimize the risk of stockouts.
Final thoughts
We hope the article helped you understand “What are stockouts?” Most customers don’t want to hear “Sorry, we’re out of stock”. Moreover, stockouts affect sales, brand value, and customer trust.
Customer frustration
If an item is not in stock when customers want to buy it, they may become frustrated. Customer retention may decrease in the event of stock outages. Keeping customers' desired items in stock can help prevent customer loss and keep customer satisfaction high.
Item schedule compensation
If an item isn't ready for a customer, the business may improve the situation by compensating for item shortages. While changing the production schedule may help fix long-term challenges, there are limited short-term options to help satisfy your customers, including:
Item count errors
When there's a difference between the actual items available and the item count customers receive, an item gap occurs. Item gaps happen for a few different reasons:
Inaccurate reports
Sometimes inaccurate anticipation of customer demand may cause a stockout. For example, if a highly anticipated toy releases, but the retailer is unaware of the toy's demand, it may become a challenge for the retailer to have continuously ready stock. Performing market research and surveys can help organizations stay up to date on in-demand items.
Delivery problems
Delivery problems from suppliers to retailers may also cause stockouts. While challenges like weather conditions or stolen merchandise are largely out of a retailer's control, delivery problems within a retailer's control may cause a stockout.
1. Update computer data
Because item gaps cause stockouts, keeping updated computer data across warehouses and retail locations can help prevent these situations. Syncing data across all warehouses allows computer systems to apply updates.
2. Establish a recheck system
Establishing a recheck system for all stock counts can help reduce the number of stockouts due to human error. For example, if your employees manually check the stock of certain items every week, establishing a recheck in the middle of every week may help reduce item gaps.
What is stockout in online stores?
A stockout is an event in which inventory is currently unavailable, preventing an item from being purchased or shipped. For online stores, a stockout can cause a lot of frustration for the customer especially if there is no indication on when the item will be back in stock and available for purchase.
Why do stockouts happen?
What causes stockouts. Stockouts happen for a variety of reasons. Factors such as underestimating customer demand, major supplier delays, and a lack of funds to purchase new inventory can all lead to products being out of stock. Many times, stockouts are inevitable and out of your control. For instance, production delays, delivery issues, unpaid ...
How does stockout affect your business?
Stockouts can significantly impact a customer’s experience and they are something you will want to focus on avoiding at all costs. Stockouts create disappointment and frustration not only for you as a business owner but for the customer who is ready to buy and may need your product quickly.
What is safety stock?
Safety stock is the excess product you keep on hand in case of an emergency or retail supply chain failure that causes a drop in inventory levels. To accurately calculate safety stock, you will need the following for each SKU:
Why is it important to keep products in stock?
But if products are constantly out of stock, it can cause a big dip in potential sales, drive customers away, and ultimately stunt business growth. In this article, we’ll go over what causes stockouts and how to prevent them from impacting long-term ...
What happens if you have a stockout?
If you have a stockout, not only will you see a major drop in conversions because there’ s nothing to buy, but the customer will most likely purchase from a competitor that has the item currently in stock. And they may continue to purchase from the competition again in the future.
Can you use historical inventory data to predict future sales trends?
By using historical inventory data to predict future sales trends, you can make better decisions on how much inventory you need in stock at a given time.
What is stockout in manufacturing?
The basic scenario for a stockout is when an item that is to be used for a customer's order or for a production order is not in stock when required. If an item is not available for manufacturing then it may be possible to change the production schedule, although there is a significant cost in this due to the changes in a machine, teardown costs, ...
What happens if you stock out?
Effects of a Stockout 1 Customer agrees to wait for the item - If the item is vital to the customer, then they may be prepared to wait. Despite the goodwill of the customer, there may be significant damage to the customer's satisfaction level. 2 Customer backorders the item - Not as ideal as when the customer agrees to wait for the order to be complete, but the order is still being fulfilled. Nevertheless, the customer's satisfaction level is still significantly reduced. 3 Customer cancels the order - If the customer is able to obtain the item from another vendor or does not need the item immediately, then the customer can cancel the order. It is still possible that the customer will order from you in the future, but their customer satisfaction level has been damaged. 4 Customer cancels the order, and is no longer a customer - This is the worst-case scenario of a stockout. However, if a customer is unhappy with the communication or information supplied by the vendor then they may be willing to cut all ties and work with another vendor.
What happens if you cancel an order due to stockout?
If a customer decides to cancel their order due to the stockout then they have probably found an alternate vendor for the item. Many companies will ensure that they have more than one source of supply for their key items; therefore, it may be easier to order from the alternate than to wait for the order to be completed.
What is the worst outcome of stockout?
Losing a customer to a stockout is the worst outcome, and comes with it the highest cost to the vendor. By a customer no longer placing any order with a vendor, every order is a cost that has to be considered. If a customer was a major purchaser of goods then the cost could be severe and put the vendor in financial difficulty.
What does "no inventory" mean?
This means that with no inventory of a certain item, production has to be stopped or a customer order will not be fulfilled. For a warehouse or inventory manager it is a scenario that they most dread and with it comes a significant cost to the company. An optimized supply chain will help you supply your customers with what they want, ...
What does it mean when a customer cancels an order?
Customer cancels the order - If the customer is able to obtain the item from another vendor or does not need the item immediately, then the customer can cancel the order . It is still possible that the customer will order from you in the future, but their customer satisfaction level has been damaged. Customer cancels the order, and is no longer ...
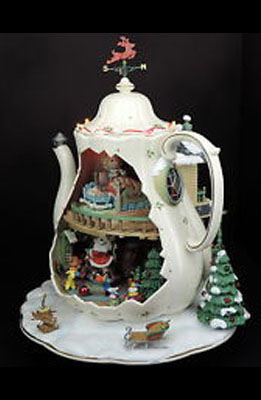
Aren’T Stock-Outs A Common Problem?
How Stock-Outs Affect Customers and Sales Teams
- Companies need to consider the impact a stock-out has on a customer.To discover in the middle of a shopping experience that the supplier is out of stock of the desired item is annoying and disappointing. You may not only lose out on the sale of that item; sometimes customers will be so irritated that they may abandon their trolley of other things a...
Does Senior Management Have An answer?
- In most instances, senior management is none the wiser as the data is most likely not available to provide metrics on achieved fill rates. If an inventory management solution exists, it can provide senior management with information such as: 1. Target and achieved fill rates per item 2. Sales history 3. Forecast of the sales lost as a result of the stock-outs 4. List of items that will potentia…