
What are the general principles of stock control?
none/very little
- this relies on a non-traditional approach to stock management such as 'Just-in-time' (JIT)
- is a difficult way of managing stock in terms of purchasing systems and management
- the firm may not obtain full discounts on smaller orders
- risks loss of customer and goodwill
What is the purpose of stock control?
- Types of stocks
- How much stock should you keep?
- Stock control methods
- Stock control systems - keeping track manually
- Stock control systems - keeping track using computer software
- Using RFID for inventory control, stock security and quality management
- Stock security
- Control the quality of your stock
- Stock control administration
What does a stock controller do?
What Does a Stock Controller Do? Stock controllers generally oversee the management, purchase, and replenishment of goods in a sales establishment to ensure maintenance of stock levels. Their job description involves maintaining accurate record of inventory and stock management systems according to set standards.
What are the methods of stock control?
Stock control and inventory
- Types of stocks
- How much stock should you keep?
- Stock control methods
- Stock control systems - keeping track manually
- Stock control systems - keeping track using computer software
- Using RFID for inventory control, stock security and quality management
- Stock security
- Control the quality of your stock
- Stock control administration
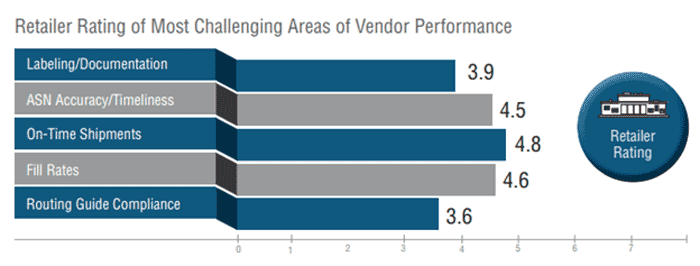
What are 4 stock control methods?
What are the methods of stock control?Just-in-time (JIT)FIFO.Economic Order Quantity.Vendor-managed inventory.Batch control.
How do you do stock control?
Set up a stock control policyIdentify stock you always need and make sure you have sufficient supply.Tighten the process of buying stock – knowing the volume sales per stock item will help you buy the right amount.Keep accurate stock records and match them to a regular physical count, at least once a year.More items...•
What are the main uses of stock control?
The purpose of stock control is to reduce the costs of holding stock while ensuring you can meet customer demand and making sure that there's enough material for production. Businesses should always have a 'safe' amount of stock so that they're able to react and cover any unforeseen issues.
How do you manage store and stock control?
Here are some of the techniques that many small businesses use to manage inventory:Fine-tune your forecasting. ... Use the FIFO approach (first in, first out). ... Identify low-turn stock. ... Audit your stock. ... Use cloud-based inventory management software. ... Track your stock levels at all times. ... Reduce equipment repair times.More items...•
What is stock control system?
Stock control, otherwise known as inventory control, is used to show how much stock you have at any one time and how you keep track of it. It applies to every item you use to produce a product or service, from raw materials to finished goods.
What is stock controller job?
A Stock Controller is responsible for ensuring that the company's stock levels meet business needs. They do this by overseeing purchases and pricing reports, replenishing levels when necessary, and monitoring shipments or internal transfers between departments within one business enterprise. Post this job for free.
What are the two types of stock control system?
There are two key types of inventory control systems.Perpetual inventory system. A perpetual inventory control system tracks inventory in real-time. ... Periodic inventory system. A periodic inventory system is kept up to date by a physical count of goods on hand at specific intervals.
What is the difference between stock and inventory?
In summary, stock is the supply of finished goods available for sale, and inventory includes both finished goods and components that create a finished product. In other words, all stock is inventory, but not all inventory is stock.
How can stock control be improved?
How to Improve Stock ControlAccurate Forecasting. ... Highlight High Sellers. ... Educate Your Staff. ... Regularly Inspect Stock. ... Maintain a Relationship with Your Suppliers. ... Consider Inventory Optimization Tools. ... Make Smart Decisions about Slow Moving and Obsolete Items. ... Resolve Issues on Time.
What is the golden rule of stock control?
What is the golden rule of stock control? In short, stock control can be the difference between making a profit or a loss. If you get it just right, it can help make your business run smoother, keep costs down and, most importantly, increase your profitability and growth.
What is MRO inventory?
MRO inventory comprises the consumable materials, equipment and supplies needed for maintenance, repair and operations activities. MRO includes items that are used in a production process but — unlike raw materials — are not incorporated into a company's finished products.
What are the 4 types of inventory?
There are four main types of inventory: raw materials/components, WIP, finished goods and MRO.
What are the methods of stock control?
To optimize stock control, there are several methods to choose from, including the following: economic order quantity (EOQ), vendor-managed invento...
Why is stock control important?
Stock control is a key part of inventory management that helps to maximize and regulate stock levels to meet customer demand while keeping warehous...
What are stock control systems?
Stock control systems are designed to help ecommerce businesses automatically track stock levels in real time, especially across multiple warehouse...
What is the golden rule of stock control?
Ecommerce businesses should always strive to keep maximum inventory of the best-sellers and reduce the volume of slow-selling stock. Historical ord...
What is stock control?
Stock control, also known as inventory management, is a series of procedures intended to manage the flow of goods through retail environments. Digital inventory systems now make up the bulk of stock control devices, but some small businesses still use pen and paper ledgers.
How do stock control tools work?
In modern retail, stock control tools take the form of a network of digital devices, including hand scanners that read bar codes and point-of-sale systems , that also scan these codes to the database computers in the manager's office. These computers store and process all location-specific data. The chief importance of these new innovations over pen and paper or mechanically printed receipts is that data can be gathered in real time by the computer and fed into a spreadsheet. These spreadsheets automate the processes of graphing and quantifying sales statistics, allowing managers to react quickly to changing demands of the market. Modern stock control tools quite literally give retailers an advantage over their competition who still use simpler methods. The downside of new digital stock control tools is that they require a fairly sizable capital investment to set up, meaning that the ticker tape cash register and ledger book are still attractive options for small time mom-and-pop operations.
Why do stock control systems matter?
The reason these systems matter is because customers who arrive at the store hoping to purchase an item that is out of stock ultimately leave frustrated, and might never return.
What is stock control?
Stock control, also known as inventory control, is the process of maintaining the appropriate quantity of stock, so a business can meet customer demand without delay while keeping the costs of holding stock to a minimum. Businesses dealing with physical products need stock to sell. The purpose of stock control is to make sure ...
Why is stock control important?
Stock control is important because it can be the difference between loss and profit.
How to control inventory?
1. Stick to a single inventory control system. It is important to ascertain from the beginning what type of inventory system would best suit your business. The two options are periodic systems or perpetual systems, of which the latter is highly recommended for accuracy and ease of use. 2.
Why is stock control important?
Why? Because any revenue that your retail business generates starts with your inventory.
What is stock control and inventory counting?
Stock control and inventory counting are processing you learn by doing. All businesses are unique, so you’ll likely cycle through some different methods before landing on one that fits your specific needs. However you do it, make sure you have the right tools to make you and your team’s lives easier.
What to check before stock take?
Before you start a stock take, check your ePOS system’s Uncategorised Inventory report to check for any items with no assigned category.#N #Well-organized inventory in your ePOS system will reduce preventable discrepancies, facilitate stock purchasing and assure the accuracy of future Inventory Count reports you may refer to.
What are the two methods of inventory management?
Proper care should be taken as to how to manage inventory counts. When counting inventory, there are two methods: physical inventory and cycle counting.
What is inventory count?
A physical inventory count (also known as a full inventory count) is when you count all of the products in your retail store in person. This is typically carried out by an assigned member of staff (or team of staff depending on how much inventory there is to count) who will count the inventory levels of each item on the sales floor and in ...
How often do retailers record inventory?
Physical inventory counts can be time-consuming and, as a result, most retailers only do them once a year.
Is inventory counting good?
Inventory counting is a good task for more junior team members, who may need to learn the ropes and be relied upon for future stock takes. If you’re flying solo, third-party inventory counters may be a viable option. They can perform the store-wide counts while you tackle the more manageable cycle counts.
What is the purpose of ordering raw materials?
Ordering the minimum amount of raw materials needed for specific production runs and reordering more frequently, in order to reduce the investment in raw materials. Creating cells in the production area, which are responsible for creating goods or sub-assemblies from start to finish.
Is there a perfect state in stock control?
There is no perfect state that can be attained in the stock control area. Instead, the planning staff is always balancing the demands of different parts of the business to attain a reasonably optimal solution - which may change the next day.
What is inventory control?
Inventory control is the management of all the items, goods, materials, and merchandise stored by a business that it plans to sell for profit.
Inventory control vs. inventory management
Though they might sound like the same thing, inventory control and inventory management do have their differences. Here’s a quick breakdown:
Importance of inventory control
Now that you understand what inventory control is, let’s look at a few top benefits of implementing it in your retail store.
Inventory control methods
The classic pen and paper approach might work if you’re a business doing single-digit monthly sales.
Types of inventory control systems
The type of inventory control system that’s best for you depends on factors like business size, capacity, your supply chain, or the type of product you sell.
Inventory control best practices
Regardless of the inventory control system you use, there are fundamental best practices you can apply to your process. Here are three worth considering:
How to manage inventory in retail?
Enjoyed this post? For more tips, check out Vend’s Complete Guide to Retail Inventory Management. This handy resource offers advice and action steps to help you: 1 Set up your products and inventory system correctly 2 Get the right people and processes in place so you can stay on top of stock 3 Figure out which of issues are causing shrink in your business so you can prevent them#N#Learn More
Why do retailers use monthly calculation?
This is an especially effective technique for retailers who frequently bring in products at the start of the season and put them on sale at the end of the season, as well as those who simply want to keep inventory fresh and exciting for their customers.
Why is inventory management important?
If you sell something with an expiration date, inventory management helps you avoid unnecessary spoilage. This also helps you avoid dead stock — those items that might not expire, but that can go out of season or style. Finally, inventory management saves you on warehousing costs.
What is OTB in retail?
Open-to-buy (OTB) inventory planning, also known as merchandise management, helps retailers stock the right amount of the right products at the right time by showing the difference between how much inventory is available and how much is needed.
What can you do with inventory management?
With a proper inventory management system in place, you can do everything from reducing your overall costs and predicting future sales to preparing your business for the unexpected and keeping your business profitable.
What does C stand for in sales?
C (low-value products, high sales frequency): These products move off the shelves more quickly and easily, making them easier to predict. Because they generate sales that are less impactful to your bottom line, they require the least amount of attention and maintenance.
Is inventory management one size fits all?
While there is no one-size- fits-all approach to inventory management, there are certain approaches that have proven to be successful that you can apply to your business to decrease your stress and increase your bottom line.
Why is stock control important?
Having stock control helps retailers make the most profit with their inventory. This gives retailers an indication on how much more or less stock they need. This, in turn, helps reduce operational and storage expenses. This is especially important for brick-and-mortar retailers because controlling the amount of stock they have on hand is directly ...
How to track inventory in retail?
Tips for Better Retail Inventory Control: 1 Using real-time retail POS software that tracks inventory movement across all channels based on actual stock levels 2 Using a barcode scanner to accurately track products as they are sold or received 3 Running inventory counts to make sure that stock levels in the POS match the quantities actually on the shelves 4 Tracking the sale of inventory items to know which products are bestsellers and which items don’t need to be re-stocked
What is a taku retail?
TAKU Retail’s inventory management capabilities mean that retailers are able to automatically see real-time inventory levels at all times, regardless of how many locations or online sales channels they are selling in. Learn more about TAKU Retail’s inventory management capabilities.
Why is a higher turnover good for retailers?
Having a higher turnover is a positive sign for retailers because it means that they are able to sell more and make more sales.
What does it mean to maintain a minimum stock level?
Maintaining a minimum stock level means stores have to keep a minimum number of products in stock to make sure they are always able to replenish their shelves easily. This is especially so with retailers during busy and uncertain seasons: this could mean extended delivery delays or stockouts.
Do retailers have to worry about running out of stock?
By always having some stock on hand and determining your ideal reorder days, retailers do not ever have to worry about running out of certain items and long lead times. Knowing what stores have in-stock may seem straightforward with a single store location.
