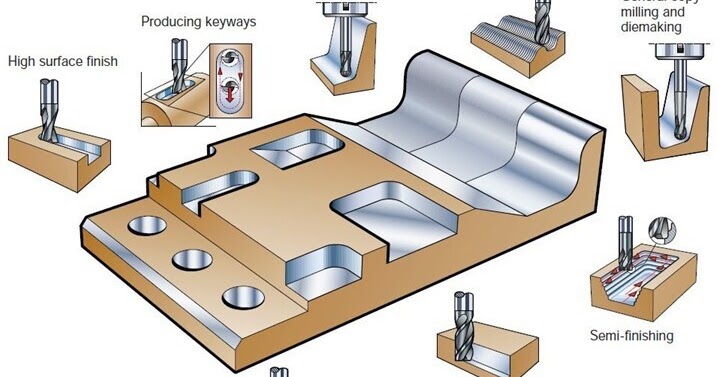
Tip: Use a Roughing end mill first to remove large areas of material then proceed with a ball nose end mill. Click here to Shop Ball Nose End Mills Roughing End Mills Great for large surface area work, roughing end mills have numerous serrations (teeth) in the flutes to quickly remove large amounts of material, leaving a rough finish.
Full Answer
What type of end mill should I use?
Use carbide end mills for harder materials and high production applications. Sometimes extra length end mills are necessary to use, but to combat deflection (bending of the bit) operate at the proper speed and feed rates and always use the most rigid (shortest and widest) end mill available for the application.
What is a double ended endmill?
A double ended endmill is like 2 endmills in one… For a little more money than one single ended endmill and a lot less money than two single ended endmills you can purchase a double ended endmill. When one end is dull, you just reverse it in the toolholder and you’ve got a brand new endmill ready to go.
What are the downsides of using endmills?
The downside is that most endmill crashes end with a broken endmill that you may or may not be able to flip around. Still, they could be an effective way to reduce your costs if you mostly dull them without breaking too many outright. This brings me to an important concept which is called “Stickout.”
How can I improve the shelf life of my endmill?
Use the whole side of the cutting edges rather than a small portion towards the tip. This will improve the shelf life of your endmill as the heat and work is distributed over a larger surface area. RPM (Revoltions Per Minute) = 3.82 x SFM (Surface Feet per Minute) ÷ endmill diameter
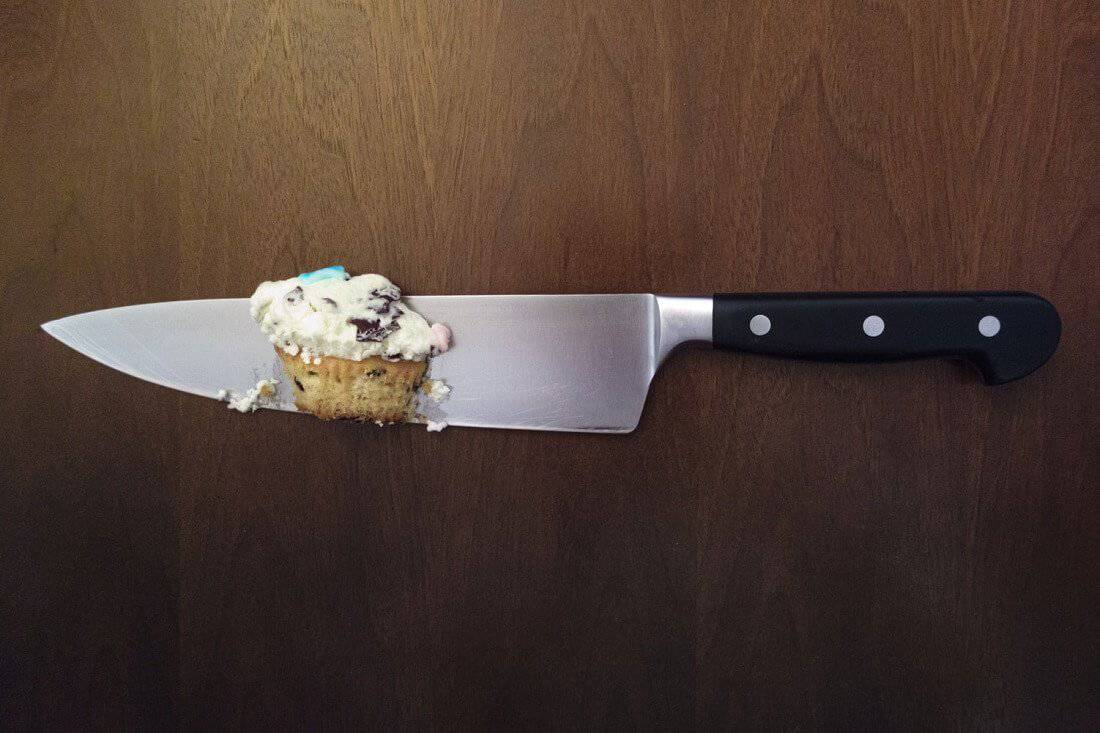
What is the best endmill for surface milling?
If you are looking for endmills for side or surface milling, then the best option is the 4 flute end mill. These mills' effect and output are very much similar to the conventional 2 flute carbide end mill. You can also use these for pocketing and slotting tasks.
What to know before buying an endmill tool?
Many factors are considered before buying the Endmill tool. But, before getting your milling tool, make sure you must know how properly it works. What is an ideal diameter, length, and flutes which you may need in your mold making? What type of endmill is required for the aluminum and the endless steel? Apart from the above guidelines, price and quality is also an important factor. Make sure after reading the above article you will buy the best endmill according to your need.
What is the essential contemplation while looking for the endmill selection?
One of the essential contemplations while looking for the endmill selection is determining the flute's proper count. Both the application and material play a crucial role in the decision of buying the endmill.
What is a high performance end mill?
From material milling to CNC functioning, high-performance end mills are used for a variety of tasks. The main application of these bits is to remove the chipped material. While these look strikingly similar to traditional drill bits, they are more multifaceted than the latter.
What is a corner radius end mill?
The following end mills type is the Corner-radius end mills, which are also called Radius Mills. These sport a square nose that has slightly curved edges or corners. This helps the bit distribute the force evenly through the bit, reducing the chances of damaging or chipping the endmills.
What is a ball nose end mill?
What is a ball nose end mill? The Ball Nose End Mill is sometimes also called ‘Ball End Mill.’ This is because they have a rounded tip and are available in both single & double-ended variants. While they can be used for conventional purposes, they also have applications in certain high-performance geometries.
What is a two flute mill?
The two-flute end mills are used in aluminum and wood. These flutes are the best for keeping this material a bit chiller and finest for keeping the evacuation a bit cooler. Still, it leaves the rougher cut.
What are the grooves in an end mill called?
Flutes are the deep spiral grooves that allow chip formation and evacuation. They are the part of the end mill anatomy that create those sharp cutting edges (sometimes referred to as “teeth”).
What is the helix angle of a mill?
General-purpose end mills typically have helix angles around 30°. Increasing the helix angle will reduce the cutting forces and the amount of heat and vibration generated during the milling process. Hence, end mills with a higher helix angle tend to produce a better surface finish on the workpiece.
What are endmills made of?
The first thing to explore is the material the endmills are made of, typically carbide or HSS, though there are a few more exotic alternatives such as powder metal. For a lot of production machine shops, the question of whether to use carbide endmills or HSS (high speed steel) seems silly.
What are roughing endmills?
First, they break up the chips making it easier to clear them out of the hole you’re cutting in. Second, the are less prone to chatter. All those serrations produce a variety of vibrations that interfere with one another instead of creation a single ringing (more often screeching, lol) tone.
What is double endmill?
A double ended endmill is like 2 endmills in one…. For a little more money than one single ended endmill and a lot less money than two single ended endmills you can purchase a double ended endmill. When one end is dull, you just reverse it in the toolholder and you’ve got a brand new endmill ready to go.
What is a center cutting endmill?
A center-cutting endmill is one that can be plunged straight down into the material. None center cutting endmills have a depression in the middle with no cutting edge, so they’ll go down a very short distance and then can be pushed no further: Center cutting on the left, non-center cutting on the right.
Why buy a non center endmill?
The only good reason to buy a non-center cutting endmill is they’re cheaper. I prefer to only have center cutting endmills around as I most often discover an endmill is not center-cutting the hard way. BTW, there is an argument to be made never to plunge endmills (well, almost never).
How many flutes are there in an end mill?
The most common options are 2, 3, or 4 flutes.
Choose Workholding Method
When it comes to workholding, not all plastic parts can be secured by clamps or vices. Depending on the material’s properties, these workholding options may damage or deform the part. To circumnavigate this, vacuum tables or other weaker holding forces, such as double sided tape, are frequently used.
Determine Heat Tolerance
The amount of heat generated should always be considered prior to any machining processes, but this is especially the case while working in plastics. While machining plastics, heat must be removed from the contact area between the tool and the workpiece quickly and efficiently to avoid melting and chip welding.
Consider Finish Quality & Deburring
The polymer arrangement in plastics can cause many burrs if the proper tool is not selected. Parts that require hand-deburring offline after the machining process can drain shop resources. A sharp cutting edge is needed to ensure that the plastic is sheared cleanly, reducing the occurrence of burrs.
Flute Count Case Study
2 FLUTE PLASTIC CUTTER: A facing operation was performed in acrylic with a standard 2 Flute Plastic Cutting End Mill. The high rake, high relief design of the 2 flute tool increased chip removal rate, but also left distinct swirling patterns on the top of the workpiece.
What happens if you run a tool too fast?
Running a tool too fast can cause suboptimal chip size or even catastrophic tool failure. Conversely, a low RPM can result in deflection, bad finish, or simply decreased metal removal rates. If you are unsure what the ideal RPM for your job is, contact the tool manufacturer.
Why is a long LOC needed?
While a long length of cut (LOC) is absolutely necessary for some jobs, especially in finishing operations, it reduces the rigidity and strength of the cutting tool. As a general rule, a tool’s LOC should be only as long as needed to ensure that the tool retains as much of its original substrate as possible.
Is roughing better than milling?
While traditional roughing is occasionally necessary or optimal, it is generally inferior to High Efficiency Milling (HEM). HEM is a roughing technique that uses a lower Radial Depth of Cut (RDOC) and a higher Axial Depth of Cut (ADOC). This spreads wear evenly across the cutting edge, dissipates heat, and reduces the chance of tool failure. Besides dramatically increasing tool life, HEM can also produce a better finish and higher metal removal rate, making it an all-around efficiency boost for your shop.
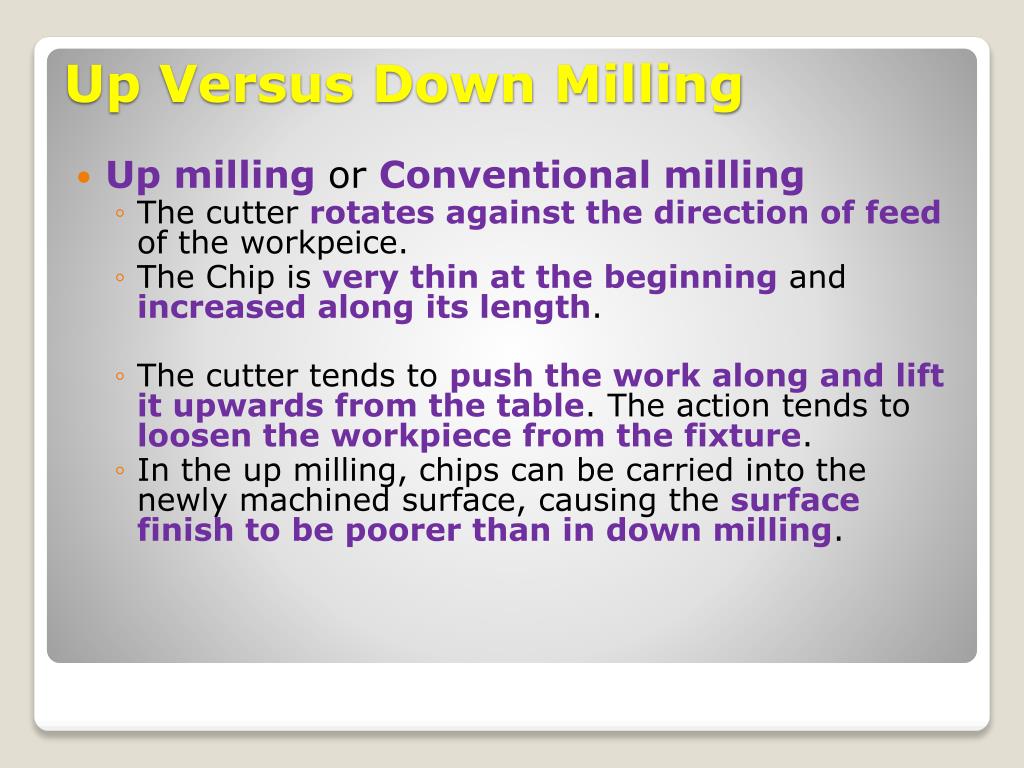