
Backordering an item means the shopper can buy the item now and receive it at a future date when the item is in stock and available. When an order contains a backordered item, it can’t be packed and shipped immediately given the lack of physical inventory at the time.
What does “on backorder” or “out of stock” mean?
When a SKU is “on backorder” that means that you are waiting for stock that hasn’t yet arrived. When a product is marked “out of stock” on your website, your customers can’t place an order.
What does it mean when something is backordered?
What does backorder mean? Backorder or back order refers to items that are not currently in stock but that are going to be soon. Customers can buy backordered items on a website, but they won’t be delivered until they are back in stock.
What is a backorder in inventory management?
Backorders are an important factor in inventory management analysis. If a company consistently sees items in backorder, then this could be taken as a signal that the company is running too lean and that it is losing out on business by not providing the products demanded by its customers.
Why do companies put some items on backorder and others on sale?
By keeping a small amount of stock in supply and the rest on backorder alleviates the need for excess/extra storage, and therefore, reduces costs. This cost reduction can be passed on to consumers, who will likely return because of a company's low prices.

Does backorder mean out of stock?
What does a backorder mean? An item on backorder is an out of stock product that is expected to be delivered by a certain date once it is back in stock. Businesses will often still sell products on backorder with the guarantee to ship them to the buyer once their inventory has been replenished.
How long does a backordered item take?
about 14 daysThough it depends on the company and product, backordered items generally take about 14 days.
Are backorders bad?
Backorders are not inherently bad. It all depends on how they are managed. They can occur for many reasons including: Unusual Demand – A common reason for backorders is an unusual demand.
Should I order on backorder?
Keeping products on backorder helps boost demand, retain and increase the customer base, and creates value for their products. A company's backorders are an important factor in its inventory management analysis.
How do you deal with backorders?
How to manage backorders:Anticipate order demand. Sometimes it's easy to forecast when an item will be in high demand. ... Diversify between multiple suppliers. ... Update product pages for backordered items. ... Provide incentives. ... Ship products separately. ... Keep customers updated.
Why are things on back order?
When shopping, customers may receive a notice that a product is on backorder, meaning that the seller currently has run out of stock, but the customer may still purchase the product. When the backordered item is back in stock, the seller will ship it to the customer.
Why do backorders happen?
A backorder is generated when an order can't be fulfilled at the time of purchase because the item is not in the seller's current inventory. However, the item is still in production or available from the distributor.
What is backorder process?
Backordering is the process of allowing your customers to place orders even if you don't have sufficient stock on hand. Businesses implement backordering when a sudden increase in sales means that products are getting sold faster than they can be stocked.
What is a backorder in inventory management?
Backorders give insight into a company's inventory management. A manageable backorder with a short turnaround is a net positive, but a large backorder with longer wait times can be problematic. Companies with manageable backorders tend to have high demand, while those that can't keep up may lose customers.
Why is it important to keep backorders?
Keeping products on backorder helps boost demand, retain and increase the customer base, and creates value for their products. A company's backorders are an important factor in its inventory management analysis.
Why is it important to keep stock in supply?
By keeping a small amount of stock in supply and the rest on backorder alleviates the need for excess/extra storage, and therefore, reduces costs. This cost reduction can be passed on to consumers, who will likely return because of a company's low prices.
Why should companies keep in contact with customers when there is a problem with fulfilling their backorders?
Companies should keep in contact with customers when there is a problem with fulfilling their backorders as promised to ensure orders aren't canceled. The sale is then recorded on the company's books as a backorder rather than a completed sale.
What is backordering?
What Is a Backorder? A backorder is an order for a good or service that cannot be filled at the current time due to a lack of available supply. The item may not be held in the company's available inventory but could still be in production, or the company may need to still manufacture more of the product.
How does backordering affect the demand?
The higher the number of items backordered, the higher the demand for the item.
What are the advantages of backordering?
Advantages of Backorders. The term backorder may conjure up negative images, but there can be positives to businesses that have these orders on the books. Keeping a large supply of stock requires storage space, which, in turn, requires money.
Defining Backordering for the online retailer
There are many terms you may come across in the eCommerce landscape when building your new business. Dropshipping, purchase order, safety stock, and carrying costs are all excellent examples. Although some words will be more crucial to you than others, it's best to have a basic understanding of the terminology you'll encounter on your journey.
Backorder Definition: What is a Backorder?
A backorder is an indication that demand for a product outweighs the supply. This could be a good sign initially for your company, but it does mean that you'll need to order more stock to manage sales orders. You could also risk losing customers who aren't willing to wait for stock levels to replenish.
Is Backorder Different from Out of Stock?
Backorders refer to a kind of out-of-stock product, but it's important to note that the definition is slightly different. Backorders are expected to be restocked and delivered to customers by a specific date. Businesses will often sell products they have on backorder and guarantee to ship them to customers when inventory is replenished.
What Causes Backorders?
Backorders can happen regardless of how well organized your supply chain and inventory management system might be. There are various issues that can lead to backorders, including an increase in demand you haven’t predicted, and changes with the way items are shipped.
Can You Reduce Backorders?
Once you understand the backorder meaning, as we described above, and you’ve seen the difference between backorder vs out of stock, you may still need to reduce your risk of backorders as much as possible.
Handling Backorders as a Retailer
Aside from being well-prepared reducing backorders as a business leader can be a process of making the right connections with other professionals and groups who can help you to stay ahead of the curve.
Getting to Grips with Backorders
Backorders can be a common part of running a business in the online retail world. It’s often difficult to predict exactly when increases in demand will take place. A backorder system is a good thing to have in place just in case you encounter this problem.
What does "backorder" mean?
Backorder meaning: When a customer places an order for an item that is not currently in stock, the customer may be informed it is on backorder and can still make payment with the promise of future delivery.
What is SOS Inventory?
SOS Inventory software will unify information from all departments – purchasing, warehousing, sales, and accounting – so you always know if you have enough product on hand to satisfy customer demand.
Can multiple vendors send purchase orders?
If required inventory amounts cannot be satisfied by a single supplier, multiple vendors can be sent purchase orders. If multiple items are required from the same supplier, they can easily be combined on the same purchase order. SOS Inventory will automatically update inventory counts when a sale takes place.
What is the difference between backorder and out of stock?
“Out of stock” means an item has no stock available for purchase and also has no current date for resupply, while 'back ordered' means an item is currently unavailable but already has a resupply date on the horizon. Unlike stock items, back-ordered items will eventually come back. It may take some time but they will eventually show up, whereas, with the other, there’s never any certainty about when or if they will.
What is a reorder point?
A reorder point is the base amount of any SKU that a business ought to have close by before they have to reorder more items. The reorder point recipe is just including your lead time request and well-being stock in days.
What does "out of stock" mean?
The answer is actually pretty simple. “Out of stock” means an item has no stock available for purchase and also has no current date for resupply, while 'back ordered' means an item is currently unavailable but already has a resupply date on the horizon. Unlike stock items, back-ordered items will eventually come back.
Benefits of Backorders
To a certain extent, backorders do give you some guarantee as to future demand.
Cons of Backordering
While some customers do not mind waiting for a product to be delivered to them even weeks later, others simply do not accept delayed delivery, and will often switch to a competitor without warning.
What causes unexpected backorders?
If backordering products is a businesses strategy that works for you, then that’s great. But sometimes other issues cause the need to backorder products unexpectedly. These issues could be:
How to avoid unwanted backorders
You can take the following steps to reduce unwanted backorders as much as possible and maybe even eliminate them altogether:
How to keep your customers happy when you have to backorder
You may often end up with a lot of backorders on your hands before you know it. Here’s how to keep your customers happy should that be the case:
What is the difference between backorders and being out of stock?
If an item is out of stock it means that the product is not in stock and there is no expected resupply date. Backordered products have a date for resupply.
Will backorders work for your eCommerce business?
When customers see the dreaded “out of stock” sign next to items they want very badly, they may never return, even if the items are back in stock a few days or weeks later.
What happens if a product is marked out of stock?
When a product is marked “out of stock” on your website, your customers can’t place an order. The backorder definition is different from meaning of out of stock because if an item is available on backorder, customers can still place an order. Rather than your normal shipping turnaround, the customer will have to wait longer for a back ordered item.
What to do when your supply chain goes out of stock?
However, sometimes your supply chain breaks down and an item goes out of stock. If you’re wondering what to do if a product is out of stock, there is a solution: backorders. You can keep your products available on backorder and allow your customers to keep shopping. Backorders aren’t ideal. Consumers don’t like to wait for the products they want. ...
What are the downsides of backordering?
What backorders may cost your business. There are, of course, some major downsides when your customers have to wait to receive an order. Cancellations. The longer someone has to wait to receive an item, the greater the chance they will change their mind. They might have second thoughts about an impulse purchase.
How to reduce backlog?
One of the ways to reduce a backlog is to process backorders quickly once you receive the merchandise. However, it can take days for your order fulfillment warehouse to process a container full of product, log it into inventory, and place it on the shelves.
What will happen to supply chains in 2020?
Supply chains break down. Weather or natural disasters can hold up transportation. In 2020, the pandemic has disrupted global manufacturing, creating shortages and delays for many companies. Combine that with a surge in eCommerce shopping, and backorders are inevitable.
What happens when you mark items as out of stock?
When you mark items as out of stock in your online store, you turn away customers who may never come back. Setting up a system for backordering allows you to keep your customers connected. Before you offer backorders, make sure you have systems in place to handle them.
What does it mean when a product is backordered?
Backordered products have been planned and ordered by the manufacturer but have not yet been produced, meaning your order will be next on the list when they are back in stock. When a SKU is “on backorder” that means that you are waiting for stock that hasn’t yet arrived.
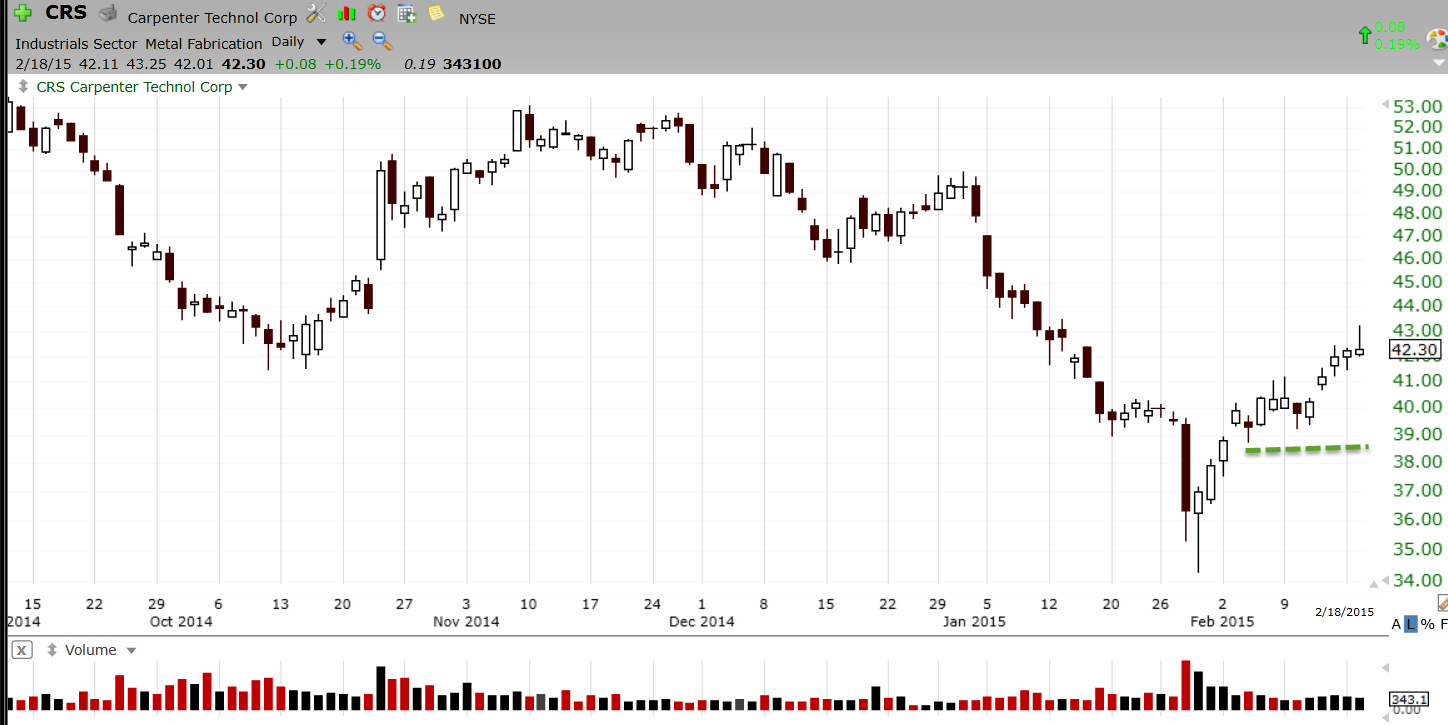