
In the context of investing, the term ' boiler room operation' refers to an outfit using high-pressure sales tactics to sell stocks to clients who are cold called or called randomly, most likely after being picked out of a phone directory.
Full Answer
What is the job description of a stockroom?
Stockroom Job Description. Companies use stockrooms to store materials used in production and finished products that aren't yet on the retail store floor. The attendants and workers who work in stockrooms manage the inventory and deliver materials to the store or production floor.
What does a retail stockroom associate do?
Retail stockroom associates are responsible for the flow of merchandise from a central point of delivery to the retail sales floor, to an internal destination, or into a shipping or delivery process. These employees can be responsible for receiving, unpacking, processing, organizing, storing, packaging, and labeling merchandise.
What is the role of inventory management software in keeping stockroom?
The role of inventory management software in keeping your stockroom in top shappe. It may not be the sexiest part of your store, and it doesn’t get a lot of customer eyeballs, but your stockroom is still a critical part of your physical location. In many ways, your stockroom acts as the headquarters of the store’s operations.
What are the requirements to work in a stockroom?
Some stockroom workers must operate heavy equipment such as a fork lift or pallet jack. Most companies require a high school diploma for a position as a stockroom worker. Experience may be required for advanced positions in a stockroom such as supervisor.
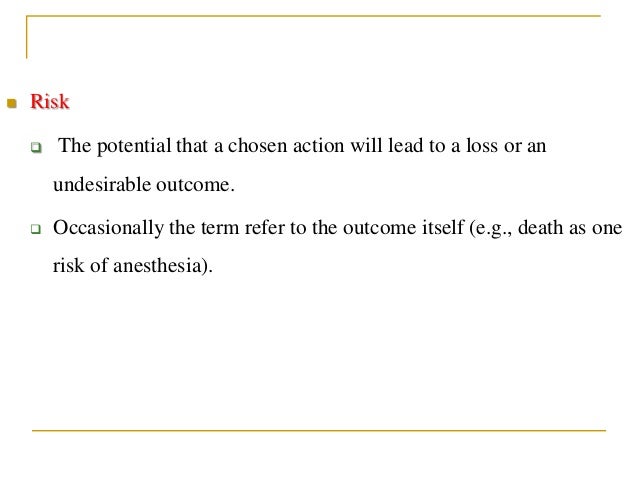
What is stockroom operation?
A stockroom associate organizes the merchandise in a retail storeroom. Job duties include receiving and unpacking deliveries, inspecting items for damage, tagging items and entering them into inventory, organizing stockroom shelves, and placing merchandise on the sales floor.
What does a stockroom operations associate do at Kohl's?
You will offer information to the customer on current merchandise assortment, store promotions and events, and execute operational processes effectively and efficiently. Your goal is to connect with the customers to solve their shopping needs making everyone feel respected, appreciated and rewarded.
What does a stockroom clerk do?
Stockroom clerks ensure that inventory arrives on time, is undamaged, and is allocated to the proper areas. They keep thorough records of items shipped or received, and track inventory changes in supply or demand. They'll additionally be responsible for maintaining a clean and safe stockroom.
What are the duties of a stock associate?
The Stock Associate will be charged with receiving and checking all incoming shipments before pricing or packing them so they can be stocked on our shelves for shoppers. A Stock Associate's responsibilities include checking the accuracy of shipments and making sure they're stocked in the correct places in the store.
How much does a stockroom operations associate at Kohl's make?
$13 per hourThe typical Kohl's Stockroom Operations Associate salary is $13 per hour. Stockroom Operations Associate salaries at Kohl's can range from $11 - $15 per hour.
How much does a seasonal stockroom associate make at Kohl's?
Kohl's Salary FAQs What is the salary trajectory of a Seasonal Stockroom Operations Associate? The salary trajectory of a Seasonal Stockroom Operations Associate ranges between locations and employers. The salary starts at $46,138 per year and goes up to $52,882 per year for the highest level of seniority.
What is another name for a stock clerk?
What is another word for stocker?night fillershelf stackerstackerstock assistantstock replenisherstore attendantwarehouse operativewarehouse worker
What is the job title for someone who stocks shelves?
StockerA Stocker, or Stock Clerk, is responsible for making sure that consumers have access to the merchandise they are looking for by organizing product displays and storage. Their duties include counting inventory, adding price tags to items and putting products on shelves according to an organized system.
What is a inventory clerk?
An Inventory Clerk is a professional who is responsible for keeping track of and managing orders in stores, warehouses and other facilities. In addition, they sign off on shipments to facilitate sales while counting current product inventory. Post this job for free.
Whats a stock assistant?
Stock control/replenishment assistants are responsible for stacking and filling shelves and display areas in supermarkets and other retail outlets. The shelves must be restocked regularly to replace the goods bought by customers.
What is an associate Stocker?
Stock associates are tasked with receiving and checking products in a store and preparing them for sale. They ensure that the correct goods are received, processed, and stored according to company rules. In addition, they are responsible for pricing and facing all offerings in a store.
How do you manage a stockroom?
Just as you meticulously planned your retail store layout, great planning of your warehouse space and stockroom is critical, too. Below are some si...
What is stockroom management important?
Stockroom management helps businesses know exactly where products are, keep an accurate count on all items, free up space for new orders, and reduc...
Why is organized inventory so important?
A good stockroom layout will help your store succeed on a number of levels:Improved efficiency for restocking shelves>More accurate and timely inve...
What's the most important part of stockroom management?
Getting a reliable POS system with inventory management features is essential for most retail stores, particularly if you have a warehouse or stock...
How to set up a stockroom?
1. Maximize your vertical space. Don’t limit yourself to your floor space. Stockrooms typically have fairly high ceilings, so build up.
Where to place most popular items in stockroom?
Place the most popular items near the front. Help your floor staff function at peak efficiency by placing your most popular items near the front of your stockroom so they can quickly grab them and get back to the floor.
What is the role of inventory management software?
The role of inventory management software in keeping your stockroom in top shappe. It may not be the sexiest part of your store, and it doesn’t get a lot of customer eyeballs, but your stockroom is still a critical part of your physical location. In many ways, your stockroom acts as the headquarters of the store’s operations.
Why is climate control important in stockroom?
Climate controlling your stockroom is essential because it helps keep all of your products in pristine condition. But it’s also really important because you’re going to have employees working long hours back there.
What are the different types of storage units?
There are many different types of storage units available to someone outfitting a stockroom. Shelving, racks, drawers, bins, cabinets, etc. The exact type (s) that will work for you will depend on your stock, of course, but it’s recommended that you invest in mobile storage units right from the beginning.
Can stockrooms leak?
Your stockroom can leak its chaos out onto the floor of your store. Every once in a while (usually around the holidays), our stockroom would become overstuffed and start spilling out onto the floor, forcing customers to navigate hanging racks and boxes on their way to the bathroom.
What is stockroom management?
Stockroom management helps businesses know exactly where products are, keep an accurate count on all items, free up space for new orders, and reduce stressful clutter. Even for small spaces, there are ways to organize a retail stockroom that can transform how you conduct your day-to-day business.
What is the importance of stockroom policies?
When creating your stockroom policies, prioritize safety. It’s vital that your team has a safe space to work in at all times. But also, implement rules that will promote cleanliness, organization, and efficiency. Most retailers opt to ban food and drink in the stockroom.
Why is inventory management important?
An inventory management system can do so much to improve your daily and long-term operations.
Do brick and mortar stores ship out?
Lastly, pay some attention to your shipping and receiving areas. Most brick and mortar retailers will have more products coming in than shipping out. But with more running an eCommerce side to their business in addition to their physical location, it’s important to plan for a designated space to ship out, too.
What is a stockroom job?
Stockroom Job Description. Companies use stockrooms to store materials used in production and finished products that aren't yet on the retail store floor. The attendants and workers who work in stockrooms manage the inventory and deliver materials to the store or production floor.
How do stock workers work?
Stock workers receive materials into the stockroom through receiving transactions. They verify the quantity of parts or products that arrive and the time of arrival. They enter this information into the inventory database, including the part numbers and the location of the items in the stockroom. When requested, stock workers issue materials to production or the store room floor. This may include a transaction out of the stockroom to the production floor. Some workers fill customer orders from the stockroom shelves, including packing and preparing the materials for shipment.
What skills do you need to work in a stockroom?
A stockroom worker must have basic math skills and the ability to perform simple transactions on a computer. Stockroom work is physically demanding and may require workers to bend and assume awkward positions. Workers may also be required to lift heavy materials from the stockroom shelves.
1. The Current State of Storeroom Organization
You know your storeroom is ineffective, but in order to quantify and justify an overhaul, you need to understand where the inefficiencies lay, and which stockroom organization methods will be most useful in rectifying them. Start by auditing your ordering, receiving, warehousing, and distribution processes. You will use this information to:
2. Production and Maintenance Schedules
Determine how much of each shift is best used for production, machine maintenance and housekeeping. It may be counterintuitive to shut down an assembly line that’s humming along in order to change a few gaskets, lubricate gears, or tune a motor. But these scheduled maintenance tasks can increase productivity significantly.
3. Warehouse Security
The best-designed space and the most stringent storeroom organization policies will go for naught if parts aren’t labeled and placed in their designated spaces and if policies are not adhered to. The pre-project audit should document what failsafe measures and gatekeeping systems are in place to prevent unauthorized access to the site.
4. Scope of Work
If it is done correctly, a storeroom organization project requires a lot of work. Before taking on the job, make sure you have the resources and inclination to see it through.
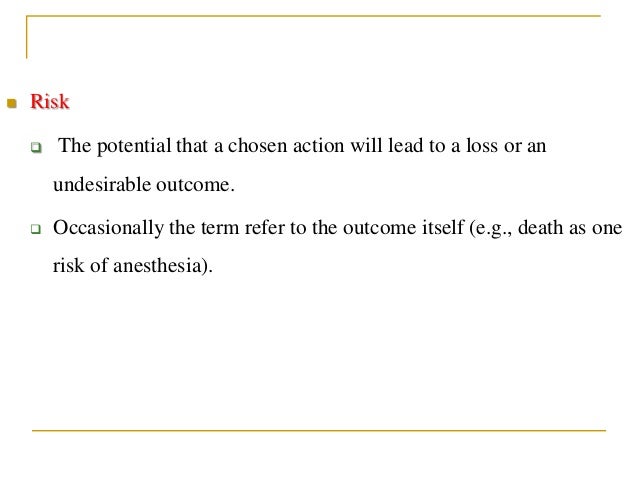