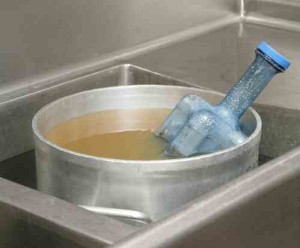
10 Fundamental Steps of Every Successful Stocktaking Process
- Schedule Your Stocktakes to Reduce Impact on Business Operations. ...
- Organize Your Stocktaking Tools Ahead of Time. ...
- Only Use Up-To-Date Inventory Data. ...
- Give Everyone Clear Goals and Responsibilities. ...
- Know What Stock You’re Counting and How You’re Counting it. ...
- Open and Count Absolutely Everything—No Guesswork Allowed. ...
- Value Your Stock Correctly. ...
What is the stock handling process?
Stock Handling Manufacturers and suppliers receive parts or raw materials for use in making finished products. These items must be tracked just as retailers track the merchandise they receive. The steps in the stock handling process include: 1. Receiving Merchandise 2. Checking Merchandise 3.
What are the fundamental steps of every successful stocktaking process?
10 Fundamental Steps of Every Successful Stocktaking Process 1. Schedule Your Stocktakes to Reduce Impact on Business Operations 2. Clean and Organize Your Stockroom Before Performing Your Stocktake 3. Organize Your Stocktaking Tools Ahead of Time 4. Only Use Up-To-Date Inventory Data 5. Give Everyone Clear Goals and Responsibilities
How accurate is your stocktaking process?
Open the box and count all of its contents to ensure it does contain that exact amount. Your stocktaking process should aim to deliver as close to 100% accurate readings as possible, which means you shouldn’t estimate or guess on any number.
How to organize the counting part of the stocktaking process?
Here’s an idea for how to organize the actual counting part of the process: – Each unit of stocktakers should be in groups of two —one person inspects the stock and calls out the amount, the second person records this and can double check the first.

How to check if a company is quoting on large jobs?
Talk regularly to your company's sales reps and other staff members to check whether they are quoting on large jobs or tendering on projects that have a high chance of success. Also find out what the customers are saying about their general level of activity.
How long does timber last?
If it's installed properly and protected from the ravages of nature, timber can last for hundreds of years.
Why are some imported timbers unavailable?
Products may become unavailable from suppliers for various reasons. Some imported timbers are particularly prone to hold-ups due to strikes or shipping delays. Other products can become scarce when there are problems at sawmills, or when government decisions change the amount of resource allocation given to a particular producer.
What are some control measures?
Some control measures may be easy to implement, such as moving a particular product to a different area of the store where it is more visible to employees of the company. Other measures may require changes to the administration system or the way sales are processed, and so involve a much more considered approach.
What is JIT in manufacturing?
The Just in time (JIT) approach to stock control is very common in manufacturing and service industries, and is sometimes used for specific products in the forest and forest products industry. The JIT approach aims to minimise the amount of stock kept on hand, so that there is just enough at any given time to satisfy the business's immediate requirements.
What is the regularity between placing one stock order and the next?
The regularity between placing one stock order and the next is referred to as the reorder cycle . There are a range of issues that will determine how often you need to order a particular product from your supplier, some of which are internal, and others external.
What is a forklift in warehouse?
forklift brings a pack of timber into the warehouse. Before it is broken open to supply customer orders, the pack number on the end will be noted and passed to the stock controller, who will mark it off in the inventory records.
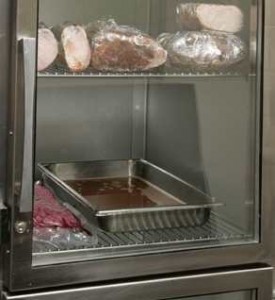