Examples of stock-out costs are:
- Lost contribution through the lost sale caused by the stockout
- Loss of future sales as customers go elsewhere
- Loss of customer goodwill
- Cost of production stoppages caused by stock-out of work-in-progress or raw materials
- Labour frustration over stoppages
- Extra costs associated with urgent, often small quantity, replenishment purchases.
How much does stock investing really cost you?
- High-yield bonds produce dividends as high as 6% to 8% and with less risk than stocks
- Tax lien investing is my favorite passive income investment and can produce up to 20% a year in income
- Rental properties regularly spin-off 8%-10% in cash rents a year
What are the costs of holding stock?
Risk and Cost of holding inventory in a firm
- Risk of price decline. Holding Inventory may increase the risk of decline in price. ...
- Risk of obsolescence. The is a risk of inventory becoming obsolescence. ...
- Purchase cost. A firm has to pay high price for managing inventory. ...
- Ordering cost. ...
- Carrying cost. ...
- Stock out (shortage) cost. ...
Can a stock ever be sold out?
There are generally three good reasons to sell a stock. First, buying the stock was a mistake in the first place. Second, the stock price has risen dramatically. Finally, the stock has reached a silly and unsustainable price. While there are many other additional reasons for selling a stock, they may not be as wise of investment decisions.
How much do stock traders cost?
- 55 trades were winners/profitable: 55 x $0.06 x 7,500 shares = $24,750
- 45 trades were losers: 45 x -$0.04 x 7500 shares = ($13,500)
- Your gross profit would be $24,750 - $13,500 = $11,250.
- Your net profit, which includes the cost of commissions, is $11,250 - commissions ($30 x 100 = $3,000) = $8,250 for the month.
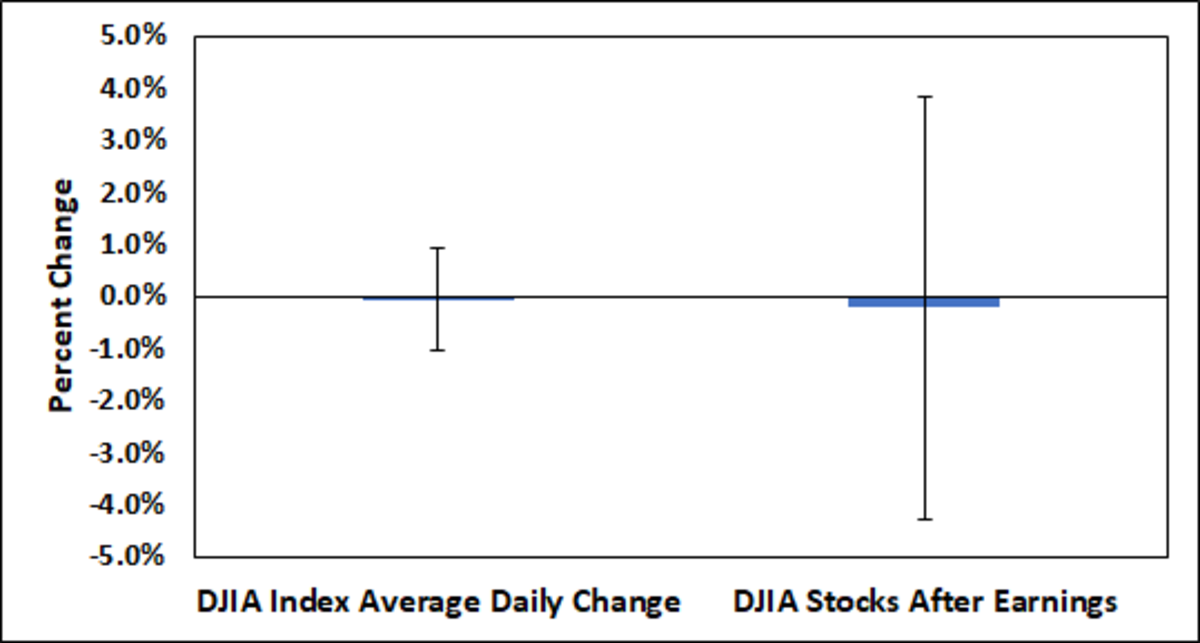
What do you mean by stock out?
What is the meaning of currently out of stock? Items that are currently out of stock, also known as a stockout, can be defined as the unavailability of specific items or products at the point of purchase when the customer is ready to buy.
What determines the cost of a stock out?
After a company goes public, and its shares start trading on a stock exchange, its share price is determined by supply and demand for its shares in the market. If there is a high demand for its shares due to favorable factors, the price will increase.
What is stock out cost in material management?
Stockout cost is the lost income and expense associated with a shortage of inventory.
What is stock out in accounting?
A stockout occurs when customer orders for a product exceed the amount of inventory kept on hand. This situation arises when demand is higher than expected and the amount of normal inventory and safety stock is too low to fill all orders.
How do you avoid stock outs?
How to reduce stock levels and avoid stock outs.Master your lead times.Automate tasks with inventory management software.Calculate reorder points.Use accurate demand forecasting.Try vendor managed inventory.Implement a Just in Time (JIT) inventory system.Use consignment inventory.Make use of safety stock.More items...
What causes stock out?
Stock-outs are caused by the following, the most significant being listed first: Under-estimating the demand for a product and, therefore, under ordering. Late delivery by a supplier. You ordered enough, but your supplier did not deliver when expected or only delivered part of your order.
What are the 4 inventory costs?
Ordering, holding, carrying, shortage and spoilage costs make up some of the main categories of inventory-related costs.
What causes stockouts and how can your prevent it?
Stockouts, and inventory shortages in general, are often caused by unexpected surges in consumer demand. However, inadequate demand forecasting or inaccurate reporting can also cause out-of-stocks.
Why are stockout costs difficult?
Stock-out costs are difficult to determine because managers have a difficult time predicting customer demand, especially if there's a high variance... See full answer below.
What are stockout costs quizlet?
What are stockout costs? • a. They are equal to inventory holding costs per unit per year.
What happens if you stock out?
Effects of a Stockout 1 Customer agrees to wait for the item - If the item is vital to the customer, then they may be prepared to wait. Despite the goodwill of the customer, there may be significant damage to the customer's satisfaction level. 2 Customer backorders the item - Not as ideal as when the customer agrees to wait for the order to be complete, but the order is still being fulfilled. Nevertheless, the customer's satisfaction level is still significantly reduced. 3 Customer cancels the order - If the customer is able to obtain the item from another vendor or does not need the item immediately, then the customer can cancel the order. It is still possible that the customer will order from you in the future, but their customer satisfaction level has been damaged. 4 Customer cancels the order, and is no longer a customer - This is the worst-case scenario of a stockout. However, if a customer is unhappy with the communication or information supplied by the vendor then they may be willing to cut all ties and work with another vendor.
What is stockout in manufacturing?
The basic scenario for a stockout is when an item that is to be used for a customer's order or for a production order is not in stock when required. If an item is not available for manufacturing then it may be possible to change the production schedule, although there is a significant cost in this due to the changes in a machine, teardown costs, ...
What happens if you cancel an order due to stockout?
If a customer decides to cancel their order due to the stockout then they have probably found an alternate vendor for the item. Many companies will ensure that they have more than one source of supply for their key items; therefore, it may be easier to order from the alternate than to wait for the order to be completed.
What is the worst outcome of stockout?
Losing a customer to a stockout is the worst outcome, and comes with it the highest cost to the vendor. By a customer no longer placing any order with a vendor, every order is a cost that has to be considered. If a customer was a major purchaser of goods then the cost could be severe and put the vendor in financial difficulty.
What does "no inventory" mean?
This means that with no inventory of a certain item, production has to be stopped or a customer order will not be fulfilled. For a warehouse or inventory manager it is a scenario that they most dread and with it comes a significant cost to the company. An optimized supply chain will help you supply your customers with what they want, ...
Why is there an increase in shipping costs?
There are increased order processing costs as the customer service staff amends the order to create a new suitable delivery date. In addition, there may be additional shipping charges if the order was part of a larger delivery, then the backorder will require special transportation.
What does it mean when a customer cancels an order?
Customer cancels the order - If the customer is able to obtain the item from another vendor or does not need the item immediately, then the customer can cancel the order . It is still possible that the customer will order from you in the future, but their customer satisfaction level has been damaged. Customer cancels the order, and is no longer ...
What is the best way to avoid stock outs?
Stock-outs could occur at any point of the supply chain. Effective Inventory management is the solution to avoid stock-outs. Regular audits of the inventory are carried out to check the frequency of stock-outs of different items.
Is stock outs costly?
Stock-outs could prove to be very costly for the companies. The subtle responses could be postponement of purchase. The more disastrous ones are the consumers may get frustrated and switch stores or even purchase substitute items (brands).
What is stockout cost?
Stockout costs are associated costs that occur due to the depletion of stored inventory, which can have adverse impacts on a company’s profits. The manifestation of stockout costs is a result of both internal and external costs.
What is external cost stockout?
Stockout external costs are those that are as a result of the consumer. In the scenario that a consumer desires to place an order but a company has inadequate or no stock, they may choose to take their business elsewhere, resulting in a loss of sale.
What is stockout in business?
Stockouts constitute a significant inventory control problem facing businesses and, by extension, consumers. A stockout happens when the number of orders for a product exceeds the amount of inventory that is stored.
What is the purpose of a thorough assessment of stock patterns?
A thorough assessment of stock patterns should be carried to determine the time when stockout occurs. The evaluation, coupled with the forecasting of your demands and the review of consumer trends, should give a clear indication of when products should be restocked.
What is systematic inventory control?
A systematic inventory control process helps to define individual roles, ensures proper implementation at each stage, and avoids stock issues. Maintaining proper communication with your suppliers ensures that everyone understands the required deadlines.
