Examples of stock-out costs are:
- Lost contribution through the lost sale caused by the stockout
- Loss of future sales as customers go elsewhere
- Loss of customer goodwill
- Cost of production stoppages caused by stock-out of work-in-progress or raw materials
- Labour frustration over stoppages
- Extra costs associated with urgent, often small quantity, replenishment purchases.
How much does stock investing really cost you?
Jan 06, 2022 · Stockout cost is the lost income and expense associated with a shortage of inventory. Stockouts can be triggered by unexpected sales or internal issues. AccountingTools
What are the costs of holding stock?
Mar 26, 2016 · In cost accounting, stockout costs represent what you lose when an item is out of stock. You need to consider both the short-term and the long-term impacts of a stockout. Assume someone sees a black-and-orange scarf on your shop’s website. When he or she stops by the store, that scarf is out of stock. Consider the impact on your business.
Can a stock ever be sold out?
Stock-out costs are costs associated with running out of stock. Examples of stock-out costs are: Lost contribution through the lost sale caused by the stockout; Loss of future sales as customers go elsewhere; Loss of customer goodwill; Cost of production stoppages caused by stock-out of work-in-progress or raw materials; Labour frustration over stoppages
How much do stock traders cost?
Feb 15, 2021 · Stockout Costs There are several costs associated with a stockout. One is the cost of rush ordering replacement products from suppliers, which may include the cost of an overnight freight delivery service. Another cost is the extra administrative cost of placing orders for replacement goods.
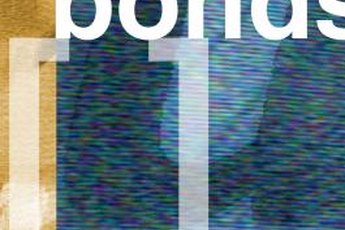
What do you mean by stock out?
noun. a state or instance of being out of stock of goods.
How do you calculate stock out cost?
How to calculate safety stockFind the following for each SKU: Maximum daily usage. ... Calculate your max (maximum daily usage x maximum lead time) Next you'll multiply the maximum daily usage by the maximum lead time. ... Calculate your average (average daily usage x average lead time) ... Subtract the two.Jul 12, 2019
What is a stock out in inventory?
Stockouts are what happen when you run out of inventory of a particular item. An out-of-stock can happen anywhere in the supply chain, but it impacts retailers' shelves and profits the most when it occurs as the customer is about to purchase.Dec 8, 2021
What are the costs that are associated with running out of stock?
6 Hidden Costs of Stockouts1: Unhappy/Lost Customers. ... 2: Lost Revenues. ... 3: Inefficiencies Drive up Costs. ... 4: Excess Inventory & Related Costs. ... 5: Backorder Costs. ... 6: Unwanted Freight Expenses. ... Balancing Cost Effective With Accuracy.Feb 6, 2017
What is the risk of a stock out?
Stockout risk refers to the exposure to loss resulting from running out of one or more inventory items, according to Business Dictionary.
How could we prevent the cost of a stock out?
How to reduce stock levels and avoid stock outs.Master your lead times. ... Automate tasks with inventory management software. ... Calculate reorder points. ... Use accurate demand forecasting. ... Try vendor managed inventory. ... Implement a Just in Time (JIT) inventory system. ... Use consignment inventory. ... Make use of safety stock.
What are the 3 costs included in product costs?
The three general categories of costs included in manufacturing processes are direct materials, direct labor, and overhead.
What are the 4 inventory costs?
Ordering, holding, carrying, shortage and spoilage costs make up some of the main categories of inventory-related costs.
What is stockout in manufacturing?
The basic scenario for a stockout is when an item that is to be used for a customer's order or for a production order is not in stock when required. If an item is not available for manufacturing then it may be possible to change the production schedule, although there is a significant cost in this due to the changes in a machine, teardown costs, ...
What happens if you stock out?
Effects of a Stockout 1 Customer agrees to wait for the item - If the item is vital to the customer, then they may be prepared to wait. Despite the goodwill of the customer, there may be significant damage to the customer's satisfaction level. 2 Customer backorders the item - Not as ideal as when the customer agrees to wait for the order to be complete, but the order is still being fulfilled. Nevertheless, the customer's satisfaction level is still significantly reduced. 3 Customer cancels the order - If the customer is able to obtain the item from another vendor or does not need the item immediately, then the customer can cancel the order. It is still possible that the customer will order from you in the future, but their customer satisfaction level has been damaged. 4 Customer cancels the order, and is no longer a customer - This is the worst-case scenario of a stockout. However, if a customer is unhappy with the communication or information supplied by the vendor then they may be willing to cut all ties and work with another vendor.
What happens if you cancel an order due to stockout?
If a customer decides to cancel their order due to the stockout then they have probably found an alternate vendor for the item. Many companies will ensure that they have more than one source of supply for their key items; therefore, it may be easier to order from the alternate than to wait for the order to be completed.
What is the worst outcome of stockout?
Losing a customer to a stockout is the worst outcome, and comes with it the highest cost to the vendor. By a customer no longer placing any order with a vendor, every order is a cost that has to be considered. If a customer was a major purchaser of goods then the cost could be severe and put the vendor in financial difficulty.
What does "no inventory" mean?
This means that with no inventory of a certain item, production has to be stopped or a customer order will not be fulfilled. For a warehouse or inventory manager it is a scenario that they most dread and with it comes a significant cost to the company. An optimized supply chain will help you supply your customers with what they want, ...
Why is there an increase in shipping costs?
There are increased order processing costs as the customer service staff amends the order to create a new suitable delivery date. In addition, there may be additional shipping charges if the order was part of a larger delivery, then the backorder will require special transportation.
What does it mean when a customer cancels an order?
Customer cancels the order - If the customer is able to obtain the item from another vendor or does not need the item immediately, then the customer can cancel the order . It is still possible that the customer will order from you in the future, but their customer satisfaction level has been damaged. Customer cancels the order, and is no longer ...
Hidden costs of stockouts
Stockout costs are generated because of stochastic character of demand (Esfandiari, Seifbarghy 2013, p. 5792). Ordered quantities vary depending on too many aspects to be fully predicted, which is one of the most important reasons for warehouse surplus.
Solutions
One of the most popular solutions of the problem may be effectively functioning stockout-costs sharing model: VMI, also known as vendor-managed inventory. This system allows the supplier to monitor the inventory levels of contracted retailers in order to replenish inventories in accordance with JIT model.
What are the costs of stockout?
One is the cost of rush ordering replacement products from suppliers, which may include the cost of an overnight freight delivery service. Another cost is the extra administrative cost of placing orders for replacement goods. A third cost is the loss of the lifetime value of a customer who has chosen to take his or her business elsewhere as a result of the stockout.
Why is stockout a problem?
A stockout causes an increased risk of lost sales, since customers are more likely ...
Can stockouts affect long term customer relations?
This can have a negative impact on long-term customer relations. A stockout condition may be intentional. For example, a seller may not have access to sufficient capital to invest in inventory, so it maintains a low inventory level and accepts the consequences of frequent stockouts.
What is the best way to avoid stock outs?
Stock-outs could occur at any point of the supply chain. Effective Inventory management is the solution to avoid stock-outs. Regular audits of the inventory are carried out to check the frequency of stock-outs of different items.
Is stock outs costly?
Stock-outs could prove to be very costly for the companies. The subtle responses could be postponement of purchase. The more disastrous ones are the consumers may get frustrated and switch stores or even purchase substitute items (brands).
What is stockout cost?
Stockout costs are associated costs that occur due to the depletion of stored inventory, which can have adverse impacts on a company’s profits. The manifestation of stockout costs is a result of both internal and external costs.
What is external cost stockout?
Stockout external costs are those that are as a result of the consumer. In the scenario that a consumer desires to place an order but a company has inadequate or no stock, they may choose to take their business elsewhere, resulting in a loss of sale.
What is stockout in business?
Stockouts constitute a significant inventory control problem facing businesses and, by extension, consumers. A stockout happens when the number of orders for a product exceeds the amount of inventory that is stored.
What is the purpose of a thorough assessment of stock patterns?
A thorough assessment of stock patterns should be carried to determine the time when stockout occurs. The evaluation, coupled with the forecasting of your demands and the review of consumer trends, should give a clear indication of when products should be restocked.
What is systematic inventory control?
A systematic inventory control process helps to define individual roles, ensures proper implementation at each stage, and avoids stock issues. Maintaining proper communication with your suppliers ensures that everyone understands the required deadlines.
What is stockout in retail?
What Is A Stockout + 9 Ways To Avoid It. Stockouts are one of the pains of inventory management. It costs retail businesses about $1 trillion every year , and customers themselves encounter stockouts as often as 1 in 3 shopping trips.
What causes stockouts?
A stockout can happen when there are discrepancies between item counts. Technical glitches, human error, or loss of goods due to theft or damage usually cause these discrepancies. For example, your FBA warehouse in the US is supposed to receive 100 units for a one-week mid-year sale, but only 70 arrived successfully, while the other 30 are declared missing. If left unresolved, you could stock out sooner than expected. Similarly, either you or your warehouse miscalculating the number of units you have in stock can mess up your item counts as well.
What happens when you have too much cash?
When you have too much cash tied up in slow-moving products and other fees, you won’t have enough money to replenish inventory for the SKUs that sell well, resulting in stockouts. Increase your profit margins by:
What is buffer stock?
The extra units that are held in inventory to reduce stockouts is called buffer stock. Buffer stock can be held at FBA or at your 3rd party warehouse but we advise a healthy split between the two. Maintaining low buffer stock levels increases your risk of stocking out. Make sure that the amount of buffer stock you keep is enough to compensate for any shipment delays and logistical problems that may occur. Read more here.
What happens if inventory doesn't arrive on time?
If your inventory doesn't arrive on time, it can again lead to stockouts. Document and verify all your orders and lead times in writing and ensure that everyone, including your supply chain manager, is on the same page at all times.
What happens if you stocked out on a bestseller?
So if you stocked out on a bestseller, your limit will likely be much lower when it comes time to restock it. Additionally, it isn’t factoring in lead times, order frequency, how often you transfer orders from third-party warehouses, and marketing plans.
How do sellers manage inventory?
Some sellers manage their inventory by waiting until Amazon tells them that they’re running out of stock. When that happens, they rush to reorder replenishments from their suppliers and then ship the inventory by air, which can become quite pricey.
Ordering Cost
Cost of procurement and inbound logistics costs form a part of Ordering Cost. Ordering Cost is dependant and varies based on two factors - The cost of ordering excess and the Cost of ordering too less.
Carrying Cost
Inventory storage and maintenance involves various types of costs namely:
Inventory Storage Cost
Inventory storage costs typically include Cost of Building Rental and facility maintenance and related costs. Cost of Material Handling Equipments, IT Hardware and applications, including cost of purchase, depreciation or rental or lease as the case may be.
Cost of Capital
The inventory storage costs as well as cost of capital is dependant upon and varies with the decision of the management to manage inventory in house or through outsourced vendors and third party service providers.
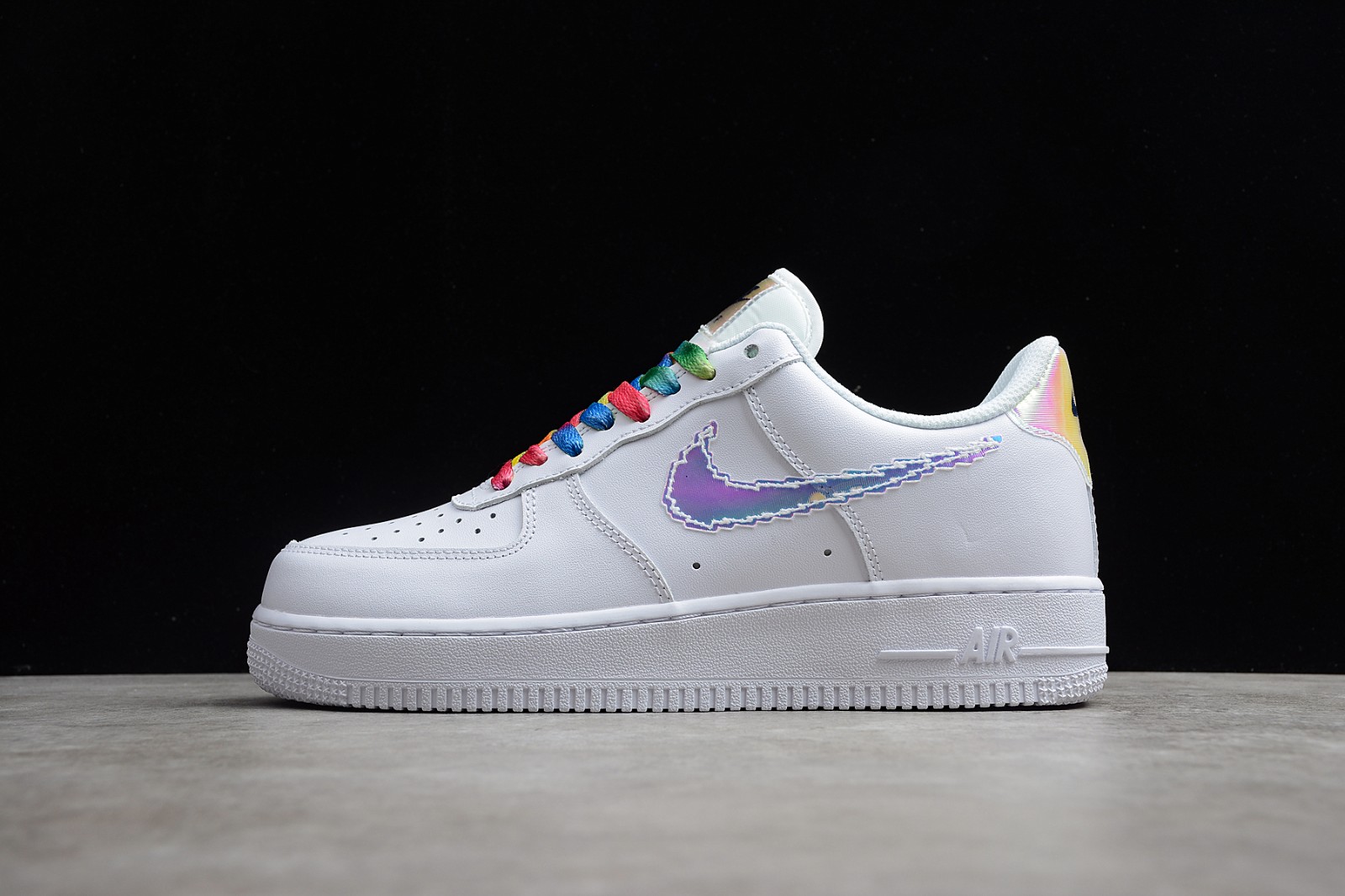