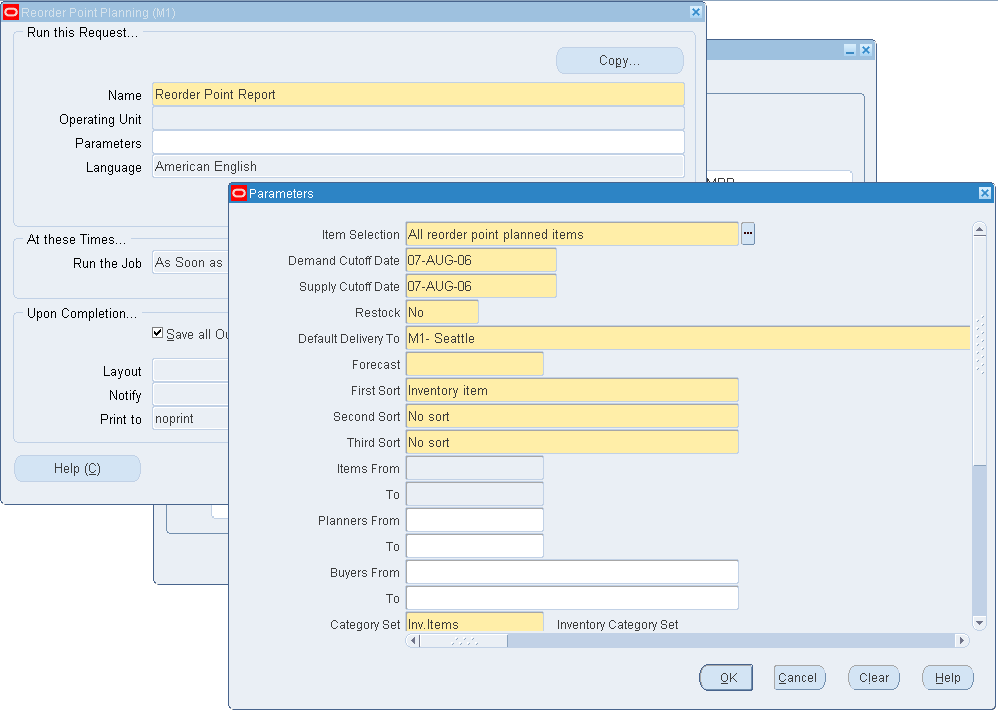
The reorder point is the level of inventory which triggers an action to replenish that particular inventory stock. It is a minimum amount of an item which a firm holds in stock, such that, when stock falls to this amount, the item must be reordered.
Full Answer
What is the inventory reorder point in inventory management?
The inventory reorder point in inventory management is the minimum level of stock for a specific product. When you reach that stock level it triggers the reordering of that particular product.
What is a reorder level of stock?
Reorder level of stock (also known as reorder point or ordering point) in a business is a preset level of stock or inventory at which the business places a new order with its suppliers to obtain the delivery of raw materials or finished goods inventory.
What is inventory ROP and why is it important?
While ascertaining the reorder level of the inventory for different SKUs, Inventory ROP determines the lead time it will take to restock so that you are not ordering goods in the nick of the time. Rather, setting an accurate reorder point allows you to offer the goods available while hanging tight for new stock.
Why do we place new orders in inventory management?
This is done in order to sustain the continuity of production in case of raw materials and the continuity of sales in case of finished goods. For this purpose, the business must set a specific level at which it should place a new order with the suppliers of inventory.
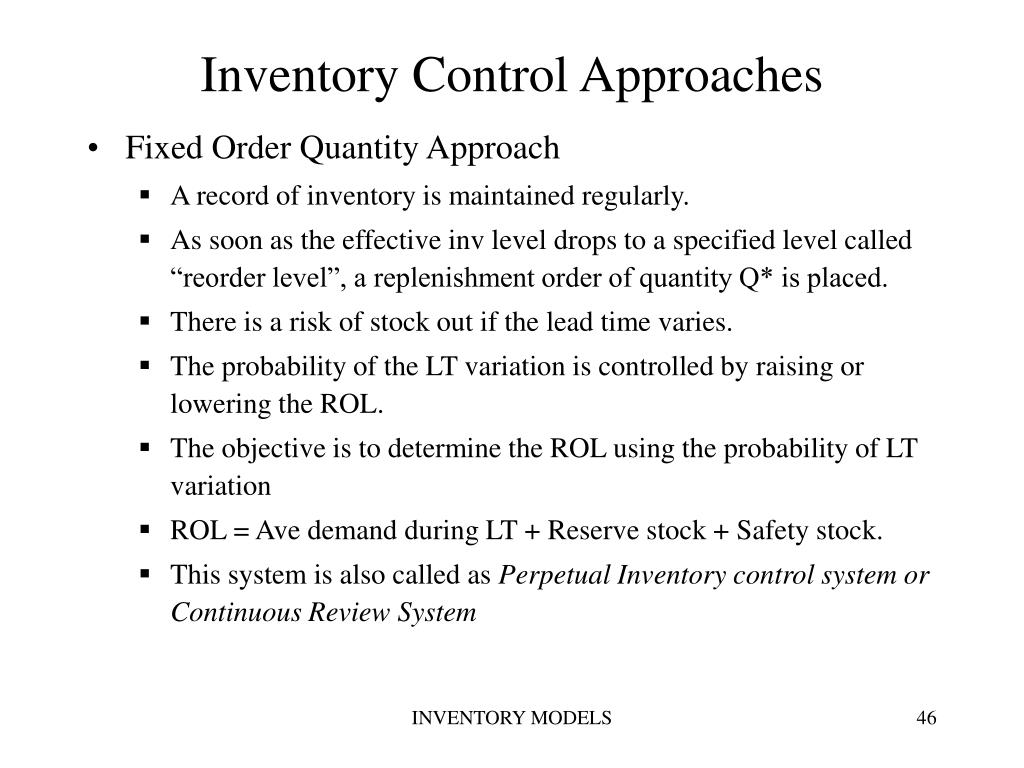
At what inventory level should reorder be made?
You should reorder when you have 40 boxes of stock left in your inventory, which is four days of stock. Given that your lead time is also four days, the new stock should arrive just in time for you to continue selling without interruption. A reorder point is crucial for effective inventory management.
What factors affect the inventory reorder point?
The two factors that determine the appropriate order point are the delivery time stock which is the Inventory needed during the lead time (i.e., the difference between the order date and the receipt of the inventory ordered) and the safety stock which is the minimum level of inventory that is held as a protection ...
What is the reorder point in the inventory control?
The reorder point (ROP) is the minimum inventory or stock level for a specific product that triggers the reordering of more inventory when reached. When calculating the reorder points for different SKUs, the lead time it will take to replenish inventory is factored in to ensure inventory levels don't reach zero.
What is the difference between reorder level and reorder quantity?
Reorder level is the stock level of a particular item of inventory, at which a firm needs to place an order for the fresh supply or replenishment of the item; whereas reorder quantity is the magnitude or the number of units to be ordered in a new purchase order for the fresh supply of a particular inventory item.
How do you know when to reorder stock?
In order to calculate reorder point, a business has to know the average unit sales per day, the average lead time and the amount of safety stock they have on hand. Multiply the average unit sales by the average lead time, then add the safety stock quantity to calculate your reorder point for a specific item.
What is stock reordering level?
The reorder level formula is that inventory level at which an entity should issue a purchase order to replenish the amount on hand. When calculated correctly, the reorder level should result in replenishment inventory arriving just as the existing inventory quantity has declined to zero.
How do you estimate reorder level?
How to calculate reorder levelIdentify your average demand. First, you'll want to identify the average demand for a product or material. ... Figure out your lead time. ... Determine whether you keep a safety stock. ... Apply the reorder level formula. ... Assess and adjust as necessary.
What is the difference between reorder point and safety stock?
An accurate reorder point means that you never get lower than your safety stock level, but a good safety stock level means that your quantity never hits zero while people are still willing to purchase the product.
What are the types of reordering systems that can be used in inventory control?
Four inventory replenishment strategiesReorder point strategy. If you use the reorder point strategy, you select a stock level that signals when it's time to reorder inventory. ... Periodic strategy. With the periodic strategy, inventory is replenished at specific intervals. ... Top-off strategy. ... Demand strategy.
What is reordering level explain its relationship with minimum and maximum stock level?
Reordering level is fixed between minimum level and maximum level. The rate of consumption, number of days required to replenish the stocks, and maximum quantity of materials required on any day are taken into consideration while fixing reordering level.
What is ROL and roq?
Firstly, let's consider the point at which stock drops to the Re-Order Level (ROL). At this point, an order is placed for the Re-Order Quantity (ROQ). If the ROQ order could be delivered instantaneously, the Maximum Stock Level you would ever have is ROL + ROQ.
What is reorder quantity?
On the other hand, reorder quantity is the number of units to be ordered while placing a new purchase order. Reorder level indicates when to submit a request for the new stock of goods and reorder quantity makes clear the number of goods to order. Reorder point involves factors like utilization of goods during the lead time, security level, ...
Why are reorder points important?
Reorder points provide businesses with greater financial understanding and allows you to keep the minimum inventory based on the customer’s demand.
How much cash is tied up in inventory?
Recent reports suggest that approximately $1.1 trillion cash, equal to 7% of theU.S. GDP, gets tied up in inventory. This means, more than the money that youcould earn on your sales, is in reality stuck in your warehouse.
Is it bad to run out of stock?
A lot of inventory is costly, however too little can result in running out of stocks, which is harmful to your growing business. The customer orders are postponed or dropped, and you start losing your loyal customers. With reorder points you will be able to maintain an optimum level of inventory. You will know exactly when to order new goods, raw materials.
Is inventory management easy?
Inventory management or inventory control isn’t an easy one when you have too much on your plate to manage. Along with that, getting the optimal level of inventory right in your warehouse is nearly impossible. Once you know when exactly to order your inventory/raw materials and the quantity of the goods, consider your job done.
What is reorder level?
Reorder level of stock (also known as reorder point or ordering point) in a business is a preset level of stock or inventory at which the business places a new order with its suppliers to obtain the delivery of raw materials or finished goods inventory.
How to calculate reorder level?
Formula: The two formulas used to calculate the re-order level are given below: 1. When the business does not need to maintain safety stock: Maximum demand or usage (in days, weeks or months) × Maximum lead time (in days, weeks or months) 2. When the business needs to maintain a safety stock:
Why is a level of safety stock set?
This is because the demand and the lead time of the goods could differ than the usual trends and in that case the business may run out of stock. So, a level of safety stock is set to avoid such a condition. It is also known as buffer stock.
Why do businesses need to maintain a certain level of raw materials?
This is done in order to sustain the continuity of production in case of raw materials and the continuity of sales in case of finished goods.
Why is the reorder level higher than the minimum level?
The reorder level of stock is generally higher than the minimum level to cover any emergencies that may arise as a result of abnormal usage of materials or unexpected delay in obtaining fresh supplies.
What does CD mean in accounting?
The latter is lower, since in its fixation no allowance is made for the margin of safety. CD = Minimum Stock or Safety Stock.
1. Reorder Stock Levels
When the quantity of materials reaches a certain level then fresh order is sent to procure materials again. The order is sent before the materials reach minimum stock level. The reordering level is fixed between the minimum level and maximum level.
2. Minimum Stock Levels
This represents the quantity that must be maintained in hand at all times. If stocks are less than the minimum level, then the work will stop due to a shortage of materials.
3. Maximum Stock Levels
It is the quantity of materials beyond which a firm should not exceed its stocks. If the quantity exceeds the maximum level limit then it will be termed as overstocking. A firm avoids overstocking because it will result in high material costs.
4. Average Stock Levels
It is the level of an average of minimum level and Maximum level. It means the average level is maintained in states.
5. Danger Stock Levels
This is the level below the minimum stock level. When a stock reaches this level, immediate action is needed to take for the replacement of stock. If the stock is reached at this level, the normal lead time is not available, and hence regular purchase procedure can not be adopted. This may result in high-cost remedial action only.
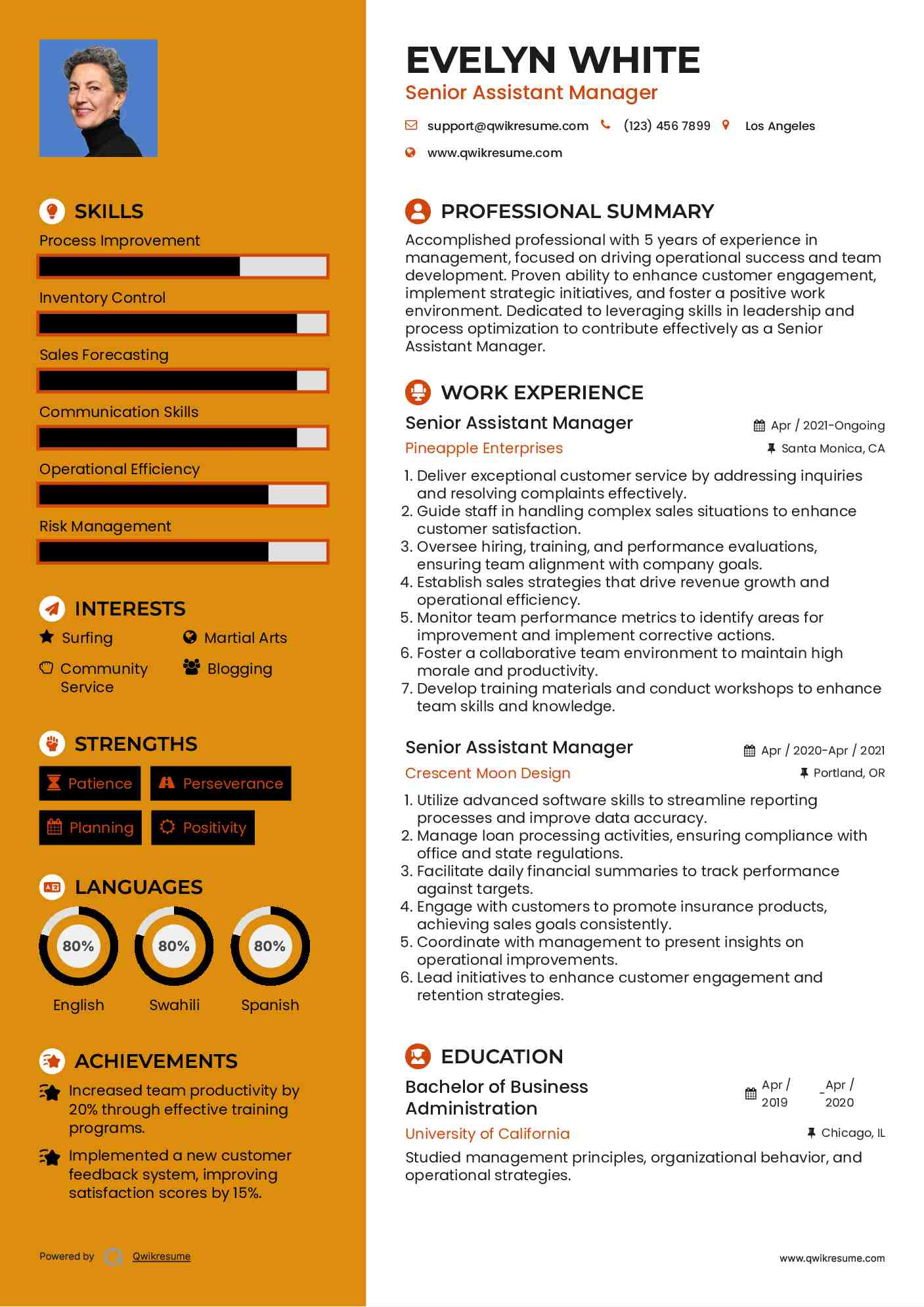
Formula
- The two formulas used to calculate the re-order level are given below: 1. When the business does not need to maintain safety stock: Maximum demand or usage (in days, weeks or months) × Maximum lead time (in days, weeks or months) 2. When the business needs to maintain a safety stock: [Maximum demand or usage (in days, weeks or months) × Maximum lea...
Example 1 – Reorder Level Without Safety Stock
- The David IT Store sells 500 laptops on an average in a week. The maximum demand in a week is 523 laptops. If, the lead time is 4.5 week then the reorder level would be: Reorder level = Maximum weekly usage × Lead time in weeks = 523 units × 4.5 weeks = 2,354 units It means that every time the number of laptops decreases to 2,354, the David IT Store must place a new order.
Example 2 – Reorder Level Without Safety Stock
- A business manufactures tires. The average demand for the business is 645 tires/week and the maximum demand is 670 tires/week. To manufacture one tire 3 kilos of rubber is required as raw material. So, the production department of the business requires a maximum of 2,010 (= 670 × 3) kilos of rubber per week. If the lead time to get rubber from the supplier is 1.5 weeks then re-ord…
Example 3 – with Safety Stock
- The following information belongs to Kim Kardashian Clothing Outlet: Usage or demand 1. Minimum demand: 390 sweaters per month 2. Average demand:420 sweaters per month 3. Maximum demand:435 sweaters per month 4. Safety stock: 120 sweaters Lead time 1. Minimum lead time: 1.2 months 2. Average lead time: 1.5 months 3. Maximum lead time: 1.75 months Req…