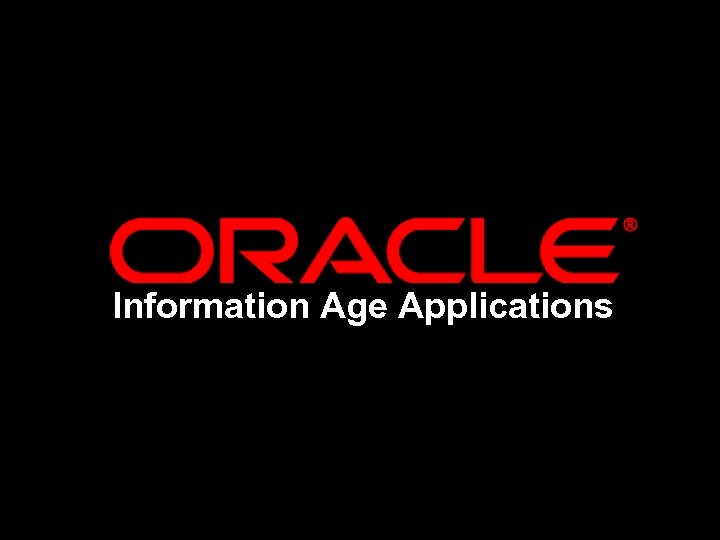
What is safety stock in SAP?
When it comes to your materials planning, it pays to have some extra raw materials laying around, an idea known as safety stock. In SAP, safety stock can be calculated and tracked in SAP Production Planning (PP). Types of Safety Stock in SAP The SAP ERPsystem offers two types of safety stocks: absolute safety stock and safety days’ supply.
What is the safety stock method used in APO SAP SNP?
If the Safety Stock field and the MRP 2 Tab in SAP ERP and the Safety time/act. cov is filled in, then the Safety Stock Method used in APO SAP SNP is SM. If only the Safety Stock field is populated, the Safety Stock Method is SB.
What is the difference between the safety stock and safety stock method?
SAP’s method of setting safety stock and safety stock calculation in APO is somewhat counterintuitive because the controls are actually in SAP ERP, while the Safety Stock Method is in APO. But merely changes based on the values entered in SAP ERP.
How do I control safety stock?
Safety Stock can be controlled in several places. These include: The location product master on the Lot Size tab, towards the bottom. Controls include (Safety stock, reorder point, maximum stock level, stock, safety stock method, service level, demand forecast error, rlt forecast error).
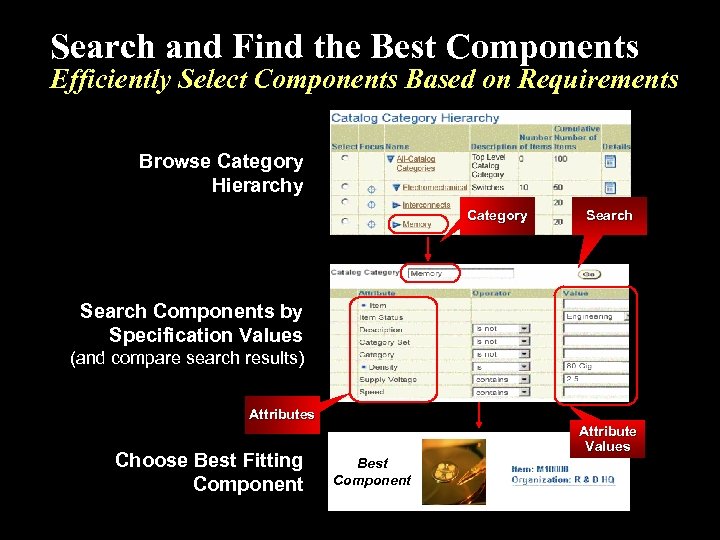
How do you solve safety stock?
To calculate safety stock, work out your average daily use for a product and multiply it by its average lead time – how long it takes, in days, to arrive once you place an order. Then subtract this number from your maximum daily use times your maximum lead time. The result is the safety stock number for that product.
How does SAP adjust safety stock?
To define the safety stock parameters, use configuration (Transaction SPRO) menu path, Logistics > Production > Material Requirements Planning > Planning > MRP Calculation > Stocks > Define Safety Stock Availability.
Where is safety stock maintained in SAP?
In SAP R/3 system , safety stock can be maintained manually or same can be calculated automatically in material master level . 1. MRP1 View : MRP Type : VM-Automatic Re-order point or VV -Forecast Base Planning.
How do you consume safety stock in SAP?
The portion of the safety stock available for planning can only be determined using the MRP group. Therefore, to determine that a certain percentage of the safety stock of a particular material is to be available for planning, this material must have been given the appropriate MRP group in the material master record.
How do you adjust stock in SAP?
On the SAP Easy Access menu, choose Accounting →Production Sharing Accounting →Processing →Manual Transfers →Stock Adjustments . The PSA Stock Adjustments screen appears. Enter data as required.
How do you check the safety stock of a material in SAP?
You enter the minimum safety stock in the material master record (MRP 2 screen). Safety Stock: In IMG -> Materials Management -> consumption Based Planning -> Master Data -> Check MRP Types (transaction code OMDQ) you use the indicator Calculate Safety Stock so that system calculates the safety stock automatically.
What is MD04 TCode in SAP?
MD04 is the materials Stock/requirements List it is essentially a listing of all the planned consumption (production reservations, sales orders etc) and all the planned receipts (purchase requisitions, shipping notifications, schedule agreements, planned orders, production orders) of your material over time.
How do you access Marc table in SAP?
Below you can view the Table Structure, columns(fields), SAP Wiki pages, discussion threads, related TCodes, FMs, ABAP Reports, BW Datasources, and Authorization Objects for MARC. You can use the transaction code SE16 to view the data in this table, and SE11 TCode for the table structure and definition.
How much safety stock should be carried in an MRP system?
There is no silver bullet when it comes to determining safety stock, but there are formulas that you can use to help you figure out the right amount to keep on hand. To help you get started on determining your safety stock levels, the 50% rule is a generally accepted starting point that businesses use.
What is safety stock level?
Safety stock is a term used by logisticians to describe a level of extra stock that is maintained to mitigate risk of stockouts (shortfall in raw material or packaging) caused by uncertainties in supply and demand. Adequate safety stock levels permit business operations to proceed according to their plans.
What does safety stock mean?
Safety stock is an extra quantity of a product which is stored in the warehouse to prevent an out-of-stock situation. It serves as insurance against fluctuations in demand.
How does safety time work in SAP?
The safety time / actual range of coverage ensures that the planned warehouse stock covers the requirements of a defined number of days. It therefore serves as a time float and thus works alongside the safety stock, which acts as a quantity float.
How does safety time work in SAP?
The safety time / actual range of coverage ensures that the planned warehouse stock covers the requirements of a defined number of days. It therefore serves as a time float and thus works alongside the safety stock, which acts as a quantity float.
What is Dynamic safety stock in SAP?
Dynamic Safety Stock = Average Daily Requirement * Range Of Coverage. The Range of Coverage Profile consists of the parameters which are maintained to calculate the Dynamic Safety Stock. The parameters maintained are based on the number of days for which the material availability is required.
How does SAP PP availability check work?
Use. During sales order processing, the availability check enables you to tell the customer if the product can be delivered on time. You can control how the availability check is carried out by setting the Availability check field in the material master.
How do you set minimum and maximum stock levels in SAP?
To set this up go to Inventory > Item Master Data > Inventory Data. On this tab under Inventory Level uncheck the box by Manage Inventory by Warehouse and then you can enter numbers for Required (Purchasing UoM), Minimum, and Maximum.
Why is safety stock not used?
Usually the safety stock will not be used in production. The purpose of the safety stock is to prevent a material shortage from occurring. In order to determine the safety stock level, you must first specify the risk of a material shortage and also the desired service level. The safety stock depends on the service level ...
What is safety stock?
Safety stock as the name suggest is the stock level till which the dead stock or stock out situation will not arise (probable figure based on past data maintained in master).
What is the purpose of safety stock?
The purpose of the safety stock is to prevent a material shortage from occurring.
What is safety stock?
Safety stock and safety stock calculation is the portion of the overall stocking position, which is designed specifically to account for variability in forecasting and variability in supply. Safety stock is not required because of lead-times or because of the volume of a forecast – it is because of the variability of either of these two components. The second most important thing to understand about safety stock is that variability is projected –it is probabilistic and, therefore, subject to error. If the variability was predictable, a lower level of safety stock could be maintained – however, variability is generally not predictable. Safety stock is greatly misunderstood and misused in the industry, where the failures concerning safety stock settings are multi-dimensional. The initial calculations are often of quite poor quality, but the initially-calculated values are often managed in a highly capricious manner.
Why are formulas correct?
The formulas are correct; to reduce inventories, the inputs – or actual reality of the supply chain (such as lead times) must be reduced. Another problem is the APICS. Give people a wide berth when they come back from an APICS conference because they may have a strange look in their eye.
Is SAP APO or ERP?
SAP’s method of setting safety stock and safety stock calculation in APO is somewhat counterintuitive because the controls are actually in SAP ERP, while the Safety Stock Method is in APO. But merely changes based on the values entered in SAP ERP.
Is variability predictable in TSL?
If the variability was predictable, a lower level of safety stock could be maintained – however, variability is generally not predictable. TSL, or target stocking level, is the overall target that is set by the system. On the other hand, safety stock is simply the specialized subcomponent of the TSL quantity that accounts for ...
Is safety stock a management or operational control?
One thing to understand about safety stock is that it is an operational control, not an executive control on the stocking level and the service level. Executives set the overall objectives and financial allocations, and objectives of the company.
Can a salesperson manually change the safety stock levels for their products?
For example, if a salesperson can manually change the safety stock levels for their products, this is often a problem. If an individual in a factory can change the products’ safety stock values related to their factor, a similar bias is usually entered into the system.
Who sets the overall objectives and financial allocations?
Executives set the overall objectives and financial allocations, and objectives of the company. Safety stock needs to be set by the business operators – or those close to product management and planning and by those with a knowledge of inventory management.
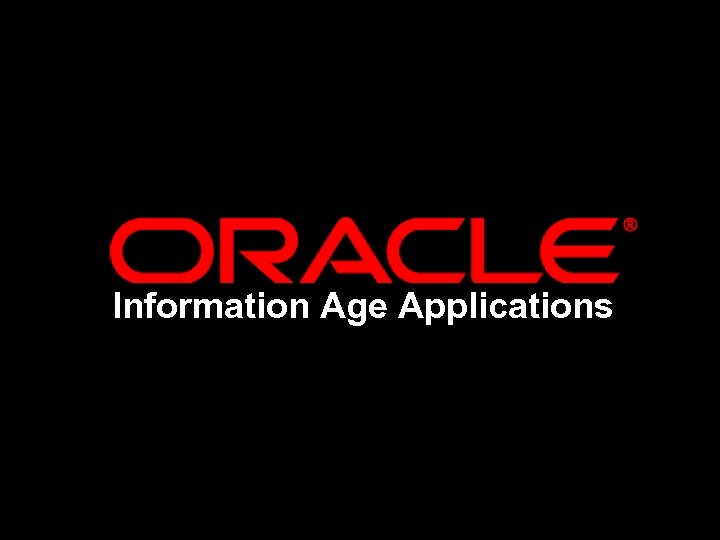