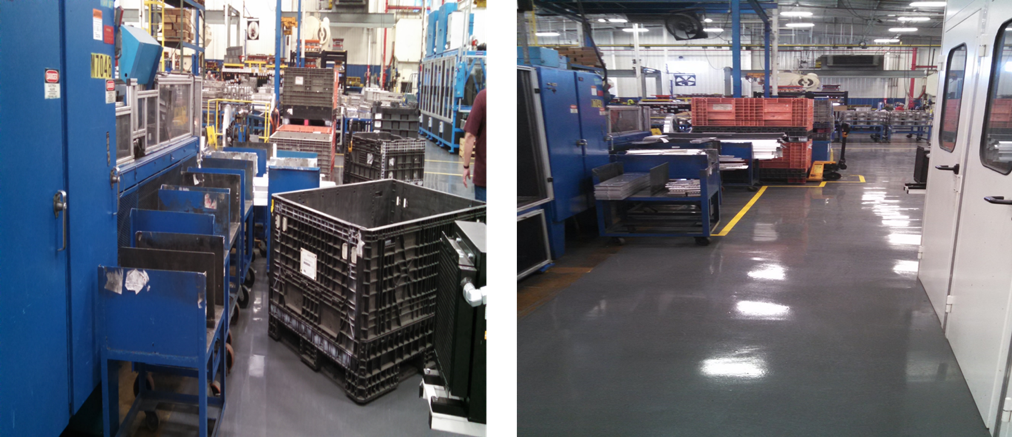
Here are 9 ways to reduce your stock and increase order efficiency:
- Use vendor managed inventory & vendor stocking programs: With the right incentives, letting VMI suppliers take the responsibility for replenishment of your inventory, because of their visibility into both their ...
- Reduce lead times: When supplier lead times are reduced below the required lead time you set it’ll help remove the requirement to hold much stock, especially consumables. ...
- Improve reliability of supply: Unreliable supply is one of the reasons for holding safety stocks. ...
- Order more frequently: This reduces cycle stock and will often cut it in half. ...
- Expedite more effectively: Solving supply chain failure quickly will undoubtedly improve service. We’ve all had AOG nightmares. ...
- Forecast more accurately: Better forecasting means lower safety stocks and higher levels of availability. ...
- Liquidate: There’s always a short-term price to pay on the profit and loss (P&L) and the balance sheet, when it’s clear that the value to be gained through liquidation is ...
- Strangers strategy: Where there’s a lot of slow moving product in the range, seriously addressing the fulfilment rules of your maintenance activities can make a big difference. ...
- Change the network configuration: The general rule is that the safety stock in the system is proportional to the square root of the number of locations. ...
- Master your lead times.
- Automate tasks with inventory management software.
- Calculate reorder points.
- Use accurate demand forecasting.
- Try vendor managed inventory.
- Implement a Just in Time (JIT) inventory system.
- Use consignment inventory.
- Make use of safety stock.
How much can you reduce stock?
Fixing a typical imbalance could reduce stock by up to 10% overall. Whether you choose one of these strategies or all 9, your primary goal is to reduce stock and increase efficiency. I challenge you today to implement one and began to make a shift of mass RFQs to structure and deliberate action to your RFQs.
How do you control stock levels?
The key to controlling your stock levels is knowing what products to carry to satisfy market demand. It’s critical to invest time (and money if required) in setting up advanced inventory forecasting models that produce accurate demand forecasts. It’s not enough to look at last year’s sales figures and expect this year’s to follow the same pattern!
How can I reduce my stock and increase order efficiency?
Here are 9 ways to reduce your stock and increase order efficiency: Use vendor managed inventory & vendor stocking programs: With the right incentives, letting VMI suppliers take the responsibility for replenishment of your inventory, because of their visibility into both their own inventory and your demand data, will always reduce your inventory.
How can I reduce my inventory levels?
There are a few things to consider when planning to reduce your inventory levels for certain items. For example, it may be worth keeping more items from suppliers that are far away or have long lead times.
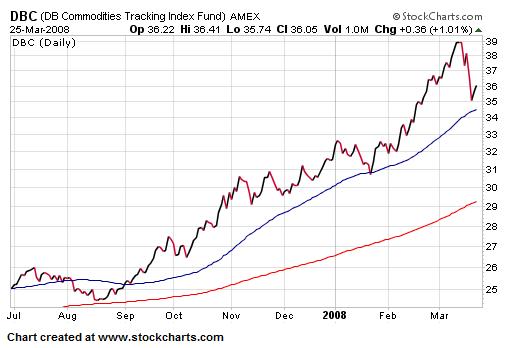
How can excess stock levels be reduced?
7 Methods for Effectively Reducing Inventories (2021)Forecast your true demand instead of your sales.Employ the Pareto distribution in merchandise assortment planning.Leverage data to perfectly time your purchasing and allocation.Optimize your logistics, warehousing, and safety stock.Automate your replenishment process.More items...•
How do you control stock levels?
Tips for Effective Stock Control and Inventory ManagementCheck All Incoming Stocks. ... Store Stocks Wisely. ... Create Clear Labels. ... Track Expiry Dates. ... Avoid Compounding Problems. ... Set Threshold Stock Levels. ... Manage Returns Effectively. ... Monitor Stocks Consistently.More items...
How do you reduce stock materials?
6 Ways to Reduce Inventory Levels1: Maintain Accurate Inventory Records.2: Establish Real-Time Reporting.3: Automate As Much As Possible.4: Manage Suppliers Collaboratively Not Confrontationally.5: Reduce Supplier Lead Time.6: Calculate Safety Stock Based on the Customer Service Level.
What is reducing stock level?
Inventory reduction is the process of lowering inventory levels to a point where they meet customer demand. Reduction of inventory is necessary to eliminate excess products, free up warehouse space, save money, and increase profits.
What are 4 stock control methods?
What are the methods of stock control?Just-in-time (JIT)FIFO.Economic Order Quantity.Vendor-managed inventory.Batch control.
What is the golden rule of stock control?
What is the golden rule of stock control? In short, stock control can be the difference between making a profit or a loss. If you get it just right, it can help make your business run smoother, keep costs down and, most importantly, increase your profitability and growth.
Why is it important to reduce inventory?
Reduced inventory saves your business carrying costs, storage costs, and transportation costs between warehouse facilities. Inventory reduction eliminates obsolete stock, which if not sold under dire circumstances, will go to complete waste and cash flow down the drain.
How do you reduce chicken stock?
Either pour into jars at this point, or if you want, what we like to do is to boil the stock on high heat for 1 hour, to reduce it by about half. This way you are storing concentrated stock, which takes less room in the freezer or refrigerator. When you are ready, pour into jars.
What do you mean by stock level?
Stock level means the level of stock required for an efficient and effective control of goods, to avoid over-and under-stocking of goods. The need of inventory control is to maintain the stock of goods as low as possible but at the same time make them available as and when required.
What are some of the ways companies can use are using to reduce the level of safety inventory required but does not adversely affect product availability?
12 Ways to Reduce InventoriesReduce demand variability.Improve forecast accuracy.Re-examine service levels.Address capacity issues.Reduce order sizes.Reduce manufacturing lot sizes.Reduce supplier lead times.Reduce manufacturing lead times.More items...•
Why cut lead times in half?
Cutting lead times in half will reduce safety stocks by about 30% for the same availability. Improve reliability of supply: Unreliable supply is one of the reasons for holding safety stocks. If delivery is guaranteed on the due date then safety stock can be reduced what's needed to cover common-cause variability.
Is liquidation of absolute stock optimal?
You are not in the conventional product sale business so liquidation of absolute or unnecessary stock is highly optimal. Strangers strategy: Where there’s a lot of slow moving product in the range, seriously addressing the fulfilment rules of your maintenance activities can make a big difference.
Why is my stock understocking?
To correct any supply issues for your company, you should first know what causes overstocking and understocking in the first place: 1. Inaccurate Data. One of the primary reasons for under- or overstocking is a lack of solid data.
What happens when you understock?
When you understock, you open yourself to several negative effects. From missing sales to losing out on discounts and shaking the loyalty of your customers, understocking can harm your company. Before you take steps to minimize understocks, you first need to know the negative effects understocking creates.
What is overstocking in inventory management?
In the inventory management world, overstocking goes by a few different names, such as excess stock, excess inventory and stock surplus. Regardless of the terminology you employ, overstocking refers to a company over-ordering inventory and having too much stock. In contrast, understocking is when a company does not have enough inventory ...
What are the problems with understocking?
The following are some of the biggest problems that understocking creates: 1 Missed sales: One of the worst effects of understocking is having to turn away customers because you no longer have an item available. Without proper stocking, you can’t provide potential customers with the items they wish to purchase. As a result, a customer will be forced to go elsewhere, and you may lose their business completely. 2 Paying more for inventory: When you buy early, typically you’ll receive more favorable prices for your inventory. As more companies get in on whatever items you’re selling, the price is going to go up. 3 Loss of discounts: Buying in bulk will often net you the best price. When you buy bulk finished products, raw materials, and parts, you typically get a much better price. When you have to reorder a smaller batch of items to make up for your understocking, the items will most likely end up costing more. 4 Shaken customer loyalty: When you don’t have enough inventory for customers, you will have to turn them away. By not having enough inventory, the customer will lose confidence in your company’s ability to meet their needs. 5 Higher shipping costs: If you’re constantly placing orders to keep up with your inventory, you’ll have to pay more in shipping and processing costs. You can avoid the shipping and processing costs by not understocking, and buying an appropriate amount for your customers in the first place.
What happens if you have too much inventory?
As you craft an inventory strategy, you’ll need to know how to minimize inventory overstocks.
What happens when you buy bulk?
Loss of discounts: Buying in bulk will often net you the best price. When you buy bulk finished products, raw materials, and parts, you typically get a much better price. When you have to reorder a smaller batch of items to make up for your understocking, the items will most likely end up costing more.
How to prevent human error in inventory?
To prevent human error, it’s best practice to automate much of the processes associated with managing your inventory. When you automate the process with an inventory management software, several tools are available to you. For example, you can set alerts that give you the most up-to-date information on a product’s status, such as when a product is about to sell out or if it has been taking too long to sell. Some inventory management software has advanced capability to predict when you need to reorder based on the current stock on hand and the sales velocity of the product.
How does stock reduction help in supply chain?
There are many financial benefits to introducing stock reduction strategies – in particular focusing on your excess and obsolete items. Carrying lower volumes of excess inventory in your supply chain can lead to lower carrying costs, such as reduced storage costs and inventory service costs.
How to prevent build up of obsolete stock?
To prevent a build up of obsolete stock it’s critical to understand where in the product life cycle each of your inventory items sit (such as growth, maturity or entering decline). As items begin to reach the end of their product life cycle you can put stock reduction strategies in place to manage slow-moving items.
Why do you need to use inventory forecast models?
You need to use accurate inventory forecast models which apply seasonality and trends to ensure any fluctuations in demand are accounted for when reordering stock. Ordering in smaller quantities is only possible if your supplier doesn’t require large minimum order quantities (MOQ).
Why is it important to get rid of obsolete stock?
If you’re carrying obsolete stock, it’s important to get rid of it to improve inventory turnover and help with stock reduction. While selling obsolete stock at a reduced price may have a negative impact on your short-term profit margins, in the long-term it will have a positive effect on your bottom line.
What is obsolete inventory?
Obsolete inventory items are those that no longer have any customer demand. This typically occurs when a product is superseded by a new model, or when tastes and fashions change and the drop in demand isn’t managed effectively.
How does lead time affect stock?
Supplier lead times have a big impact on the amount of stock you hold. For example, if lead times are long or continually fluctuate, you’ll need to carry more safety stock to cover the risk of run-out while you wait for your delivery.
Why do businesses carry surplus stock?
For businesses that carry non-perishable goods it’s tempting to order and carry surplus stock to help meet market demand and hit order fulfillment targets. In some circumstances carrying excess stock can be a good thing: having all items in stock helps avoid costly back orders and keeps customers happy. However, holding too much can have ...
How to reduce inventory?
An advanced planning and scheduling system can help with inventory reduction through: 1 Optimized Capacity Plans - Know forecast load-versus-capacity including equipment, tooling, and labor constraints. Optimize automatically to maximize the KPIs of interest for your organization. 2 What-If Scenarios - These types of scenarios allow you to evaluate your abilities to meet variable forecasts. You can simulate evolving or adding equipment and employee skill extensions to determine whether you will be able to meet increases in demands. 3 Enterprise Capacity Visibility - See workload and capacity at any level: company-wide, plant-by-plant, departmental, or even down to the resource. Various reports can identify which items are taking most of the critical resources times. 4 Just-In-Time Scheduling - One of the most well-known strategies for reducing inventory is to use a Just-In-Time strategy for production. An APS system allows you to easily schedule operations so that jobs will be completed just when they should to ship out. This reduces the number of WIP items and finished goods that need to be stored.
What is inventory reduction?
When executed properly, inventory reduction will reduce storage costs, production costs, and will prevent items sitting in inventory to become obsolete before they are sold.
Why is it important to choose suppliers that have fast, reliable, and accurate lead times?
It is important to choose suppliers that have fast, reliable, and accurate lead times to allows you to order smaller quantities without the risk of stock-outs. Therefore, establishing an excellent relationship with your supplier can optimize production and reduce inventory through an efficient supply chain.
Why is inventory management important?
Proper inventory management is crucial to be able to promptly meet customer demands without having high costs related to holding too much inventory. There are a few things to consider when planning to reduce your inventory levels for certain items.
What does it mean to have high inventory?
Having high levels of inventory has its advantages and disadvantages. On one hand, high inventory means that you have a product ready to ship out at all times. On the other hand, high inventory means that you will have increasingly high carrying and holding costs.
Why do we carry safety stock?
Carry safety stock to reduce risk of stock outs. Safety stock, also called buffer stock, is the layer of inventory kept to prevent stockouts and back orders in situations where the forecast is exceeded or supply is delayed.
What is inventory policy?
Inventory policies ensure you’re stocking the right goods in the right quantities – a must for good inventory control in the warehouse. Make sure you have a set of ‘rules’ for every SKU you carry. Inventory classification, such as
Can you optimize stock levels?
It’s impossible to optimize your stock levels without considering supply and demand variables. Effective inventory control techniques therefore rely on stock optimization tactics. Many businesses use standard ERP or WMS systems to execute their stock control procedures while others still resort to spreadsheets.
What is Out of Stock?
Call it a stock-out, oversell, or out of stock (OOS), it happens when you have a product sale that you cannot fulfill.
How Do You Prevent Out of Stock Problems?
So, how do you prevent out of stocks from hurting your business? Here are the steps that can help:
Why Is Preventing Out of Stocks Important?
Too many out of stocks can devastate brand trust and increase customer service costs. For eCommerce sellers, it can result in a loss of customer confidence in doing business with your company. In some cases, the effects of stock out can result in penalties for online marketplaces including shutting you off.
Common Questions About Preventing Out of Stocks
Here are some of the common questions that companies ask when it comes to preventing out of stocks:
Conclusion
Strategies on how to prevent stockouts can make a significant difference in your profit margins and overall bottom line.
How to reduce inventory shrinkage?
However, the good news is that inventory shrinkage can be greatly reduced by putting some simple processes in place. Implement a double-check system. One of the most straightforward ways to prevent inaccuracies in inventory management and stocktake is to have more than one person do a check when accepting inventory, signing off on invoices, etc.
Why is inventory shrinking?
Some of the biggest culprits of inventory shrinkage are theft, damage to stock, and mismanagement of inventory. Inventory shrinkage can create major problems for businesses because it can result in a loss of sales and profits.
How much did inventory shrinkage cost in 2015?
In fact, the 2016 National Security Survey found that inventory shrinkage costs businesses a whopping $45.2 billion in 2015. Loss of inventory also makes it difficult to measure the number of times inventory is sold or used in a defined period, also known as inventory turnover.
Why is stock control important?
Stock control is important because it can be the difference between loss and profit.
How to improve liquidity?
Purchasing should be based on sales history and demand forecasting. Ordering less stock more frequently. This can improve liquidity without reducing sales. Consider the impact of marketing and promotion. Before launching a sales promotion, make sure you have enough stock to meet an increase in demand.
What is stock control?
Stock control, also known as inventory control, is the process of maintaining the appropriate quantity of stock, so a business can meet customer demand without delay while keeping the costs of holding stock to a minimum. Businesses dealing with physical products need stock to sell. The purpose of stock control is to make sure ...
How to control inventory?
1. Stick to a single inventory control system. It is important to ascertain from the beginning what type of inventory system would best suit your business. The two options are periodic systems or perpetual systems, of which the latter is highly recommended for accuracy and ease of use. 2.
