
- Gain better visibility into your inventory.
- Consider upgrading your WMS.
- Track all inventory by SKUs and bin location.
- Optimize slotting practices.
- Connect all systems.
- Base safety stock on actual economics.
- Take advantage of newer shipping options, including drop shipping.
How do you reduce safety stock in a warehouse?
· As explained by Supply Chain Management Review, leaders should utilize data and follow these tips to reduce safety stock: Gain better visibility into your inventory. Consider upgrading your WMS. Track all inventory by SKUs and bin location. Optimize slotting practices. Connect all systems. Base ...
What is safety stock and how to use it?
How to Reduce Your Safety Stock Using the 80/20 Rule. The 80/20 rule is often used in parts inventory management to identify the 20% of inventory that produces 80% of the profits. (For a more in depth definition of this phenomenon, read another blog we wrote about the 80/20 rule here .) A variant of this rule, called ABC analysis, is commonly used to split inventory into three …
What happens if you don’t maintain safety stock?
· 3. Letting Safety Stock Decline as Supplier Lead Time Reduces Safety stock helps to address variability in your supply chain and demand, so supplier lead time should not impact your safety stock, only your cycle stock. You should always safeguard your inventory by looking at the standard deviation time.
Why is it difficult to calculate safety stock levels?
· 10 Reasons to Keep Safety Stock Offset Demand Uncertainty Fluctuations in demand are among the primary reasons to maintain safety stock. Many factors... Avoid Stockouts Safety stock can help companies reduce the risk of completely running out of a certain product and... Minimize the Effects of ...
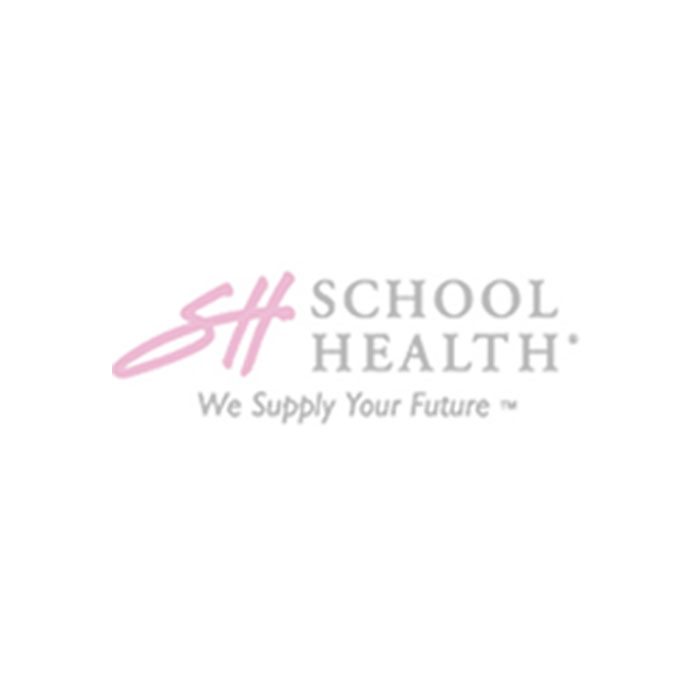
How do you manage safety stock?
To calculate safety stock, work out your average daily use for a product and multiply it by its average lead time – how long it takes, in days, to arrive once you place an order. Then subtract this number from your maximum daily use times your maximum lead time. The result is the safety stock number for that product.
What are the ways to reduce inventory?
Here are the 7 steps for effectively reducing inventories:Forecast your true demand instead of your sales. ... Employ the Pareto distribution in merchandise assortment planning. ... Leverage data to perfectly time your purchasing and allocation. ... Optimize your logistics, warehousing, and safety stock.More items...•
What causes safety stock to increase?
One of the main variables when calculating safety stock is the service level. As shown in the graph, safety stock increases with the customer service level. When the service level values reach above 95% the safety stock number increase exponentially.
What are the factors affecting safety stock?
Recalling that safety stock is a function of three main factors: uncertainty in the forecast, the number of says to cover (order period), and the confidence factor of the product.
Why should we reduce inventory?
Reduction of inventory is necessary to eliminate excess products, free up warehouse space, save money, and increase profits. Inventory reduction is also one of the most effective cost reduction strategies in inventory management.
How do you reduce excess and obsolete inventory?
There are several ways to handle obsolete inventory. You can sell them at a discount, bundle them with other products, liquidate them through surplus resellers, try to remarket them to a different audience, or do a complete inventory write off.
How does safety stock improve a company's customer service level?
Safety stock is when a business holds products in reserve to safeguard against any unforeseen shortages or product demands. It allows you to overcome any variables in your supply chain, and increase your customer service level.
What is ABC method of inventory control?
ABC analysis is a method in which inventory is divided into three categories, i.e. A, B, and C in descending value. The items in the A category have the highest value, B category items are of lower value than A, and C category items have the lowest value. Inventory control and management are critical for a business.
Does increasing lead time increase safety stock?
Safety stock helps to address variability in your supply chain and demand, so supplier lead time should not impact your safety stock, only your cycle stock.
What is safety stock example?
Examples of Safety Stock Suppose a company has a team to research the market demand, and it has estimated that the demand for an umbrella is nearly one thousand units every month. As a precaution, the company can decide to have one hundred units as safety stock because the demand is never constant.
How does lead time affect safety stock?
For cycle service levels above 50 percent but below a threshold, reducing the lead time variability increases the reorder point and safety stock, whereas reducing the lead time decreases the reorder point and safety stock.
What is safety stock in MRP?
Safety Stock is the quantity of stock held to satisfy unexpectedly high requirements in the stocking-up period. The purpose of the safety stock is to prevent a material shortage from occurring.
Which strategy is used to reduce inventory cost?
Just-In-Time Scheduling - One of the most well-known strategies for reducing inventory is to use a Just-In-Time strategy for production. An APS system allows you to easily schedule operations so that jobs will be completed just when they should to ship out.
How do you adopt the six means to reduce inventories?
6 Ways to Reduce Inventory Levels1: Maintain Accurate Inventory Records.2: Establish Real-Time Reporting.3: Automate As Much As Possible.4: Manage Suppliers Collaboratively Not Confrontationally.5: Reduce Supplier Lead Time.6: Calculate Safety Stock Based on the Customer Service Level.
What are types of inventory?
There are four main types of inventory: raw materials/components, WIP, finished goods and MRO.
What Exactly Is Safety Stock?
Safety stock refers to excess inventory capped within a warehouse or other facility to avoid the problems associated with a product being out of stock, explains Supply Chain 24/7. In today’s world, if your business does not carry or have a given product in stock, the customer can find it on Amazon. It is that simple.
Challenges Associated With Excess Safety Stock
Safety stock might not seem like a big problem, but it does lead to difficulties within supply chain visibility and efficiency. Some challenges include:
How to Reduce Safety Stock With Data
It is possible to reduce safety stock through the application of data. For example, the use of data and connected inventory (including the use of voice-enabled systems) increases the accuracy within inventory reporting.
Reduce Your Safety Stock With the Right WMS
Safety stock is a necessary evil in supply chain management. No one knows when manufacturers or market fluctuations will suddenly render your inventory obsolete or place new demand for items rarely restocked.
Is safety stock a problem?
Safety stock might not seem like a big problem, but it does lead to difficulties within supply chain visibility and efficiency. Some challenges include: Safety stock lowers the efficiency of your inventory management strategy. It relies on outdated processes and data.
How does safety stock affect supply chain?
Safety stock might not seem like a big problem, but it does lead to difficulties within supply chain visibility and efficiency. Some challenges include: 1 Safety stock lowers the efficiency of your inventory management strategy. 2 It relies on outdated processes and data. 3 It increases carrying costs for your organization. 4 While it eliminates concern over stockouts, it fails to leverage advanced order fulfillment and shipping models.
Is safety stock a necessary evil?
Safety stock is a necessary evil in supply chain management. No one knows when manufacturers or market fluctuations will suddenly render your inventory obsolete or place new demand for items rarely restocked.
Can a dedicated warehouse management system reduce safety stock?
However, the application of data and a dedicated warehouse management system (WMS) can successfully reduce safety stock.
Is it important to have a safety stock?
Ensuring that you have safety stock seems like a win-win, but it’s important to be aware of the risks related to safety stock. It’s possible to over-optimize stock levels, which isn’t always the best approach. Here are 4 common risks related to safety stock that you need to be aware of and factor into your safety stock calculation.
Why do retailers use safety stock?
One of the main reasons that retailers and manufacturers implement a safety stock strategy is to prevent stockouts. Stockouts are usually caused by: Changes in consumer demand.
What is safety stock?
Safety stock is simply extra inventory held by a retailer or a manufacturer in case demand increases unexpectedly. This means it’s additional stock above the desired inventory level that you would usually hold for day-to-day operations.
What causes stockouts?
Stockouts are usually caused by: Changes in consumer demand. Incorrect stock forecasts. Variability in lead times for raw materials. Trying to plan for these variables and maintain a target inventory level can be difficult. However, this is where a safety stock formula comes in.
How does running out of stock affect your business?
Some of the direct impacts on your business include: Loss of revenue. Loss of gross profit.
What is service level in inventory?
Service level is the probability that the amount of inventory on hand during the lead time is sufficient to meet expected demand – that is, the probability that a stockout will not occur. The uncertainty of supply and demand makes it difficult to calculate the amount of stock needed to satisfy customers needs while avoiding stockouts.
Do stock outs always occur?
Stock-outs will always occur, no matter how much you want to prevent them. The safety stock formula is there to prevent the majority of stock-outs, but not all of them. Service level plays a key factor when calculating safety stock which is what you are trying to maintain.
What Is Safety Stock?
Stock inventory usually consists of cycle stocks, or the inventory that is expected to be sold within a given period, and safety stock. Safety stock acts as a buffer amount that accounts for uncertainties such as:
How Can Safety Stock Improve Inventory Management?
Effective inventory management relies on the cushion that safety stock provides. Tracking current stock levels accurately while considering present and future market conditions and accounting for supply lead times is just the start of effective inventory control.
Why Do Businesses Need Safety Stock?
Running out of stock is an expensive issue for businesses across the globe. Stockouts result in $984 billion worth of lost sales worldwide, with North American companies alone losing $144.9 billion, according to a study by IHL Group.
How to Calculate Safety Stock
Safety stock is about more than just having a few extra units available. Different formulas help inventory managers determine how much safety stock they need and calculate some critical variables.
Complementary Formulas
These equations provide additional information to supplement safety stock calculations. They can be used to ensure that each aspect relating to safety stock is accounted for.
Common Safety Stock Challenges & Risks
Safety stock is a valuable tool to combat stockouts, but it can have some disadvantages. There are a few factors inventory managers need to consider when developing safety stock strategies.
Safety Stock Examples
Here's how safety stock works in practice: A snow shovel manufacturer knows that demand is low during the warmer months but can fluctuate significantly in the winter depending on several hard-to-predict aspects of the weather.
What is safety stock?
Safety Stock is defined as the additional quantities of goods stored as a safety net above the required amount to prevent going out of stock due to emergencies. An example of emergency is when sold off goods undergo damage on their way to be delivered. In such a case, safety stock can be used to ensure that the customer receives ...
Why are stocks bought and stored during good harvests?
During good harvests, stocks are bought and stored to keep prevent prices from falling below price levels or a target range, while stocks are released during harvests to prevent prices from rising above price levels or a target range. read more. and is obtained above the normal forecasted level.
What is a 95% service level?
A 95% service level means that there may be a stockout in 5% of the cases. A high service level increases the business’s cost to avoid stockout, but many firms do it nonetheless.
Why is safety stock important?
It is important for businesses to have safety stock on hand to reduce the risk of dealing with a stockout.
What is safety stock?
Safety stock is an inventory management best practice that is relevant to any business that deals with inventory. This ranges from manufacturing to consumer goods. That said, there is a fine line between having the optimal safety stock for a rainy day and overstocking (we don’t want that).
What is standard deviation in safety stock?
Standard Deviation: In a safety stock formula, it often measures the variance of your lead time. Also, keep in mind the difference between cycle stock and safety stock. The former is the inventory expected to be bought by consumers, while safety stock is a sort of margin of error to dip into when things go wrong.
What happens if you cancel a website because you are out of stock?
Similarly, if you are forced to cancel or delay fulfillment because you are out of stock, it ruins their experience with your brand. They'll give their money to someone else instead.
How to calculate standard deviation?
To calculate the standard deviation, you need your expected lead time and the actual time the shipments took. Then write down the variance of each shipment, which is how many days over or under the expected time it took. Positive numbers are late, and negative numbers are early.
How long does it take to run a business that sells physical goods?
Running a business that sells physical goods is all about inventory optimization. It can take months or years to get that supply chain ecosystem running smoothly and on time. Safety stock prevents your sales from coming to a complete standstill when delivery or manufacturing is slower than planned.
How to prevent build up of obsolete stock?
To prevent a build up of obsolete stock it’s critical to understand where in the product life cycle each of your inventory items sit (such as growth, maturity or entering decline). As items begin to reach the end of their product life cycle you can put stock reduction strategies in place to manage slow-moving items.
Why is it important to get rid of obsolete stock?
If you’re carrying obsolete stock, it’s important to get rid of it to improve inventory turnover and help with stock reduction. While selling obsolete stock at a reduced price may have a negative impact on your short-term profit margins, in the long-term it will have a positive effect on your bottom line.
Is it good to carry excess stock?
In some circumstances carrying excess stock can be a good thing: having all items in stock helps avoid costly back orders and keeps customers happy. However, holding too much can have a number of negative implications, such as high carrying costs, over-investment in stock and poor cash flow.
How does stock reduction help in supply chain?
There are many financial benefits to introducing stock reduction strategies – in particular focusing on your excess and obsolete items. Carrying lower volumes of excess inventory in your supply chain can lead to lower carrying costs, such as reduced storage costs and inventory service costs.
What is obsolete inventory?
Obsolete inventory items are those that no longer have any customer demand. This typically occurs when a product is superseded by a new model, or when tastes and fashions change and the drop in demand isn’t managed effectively.
