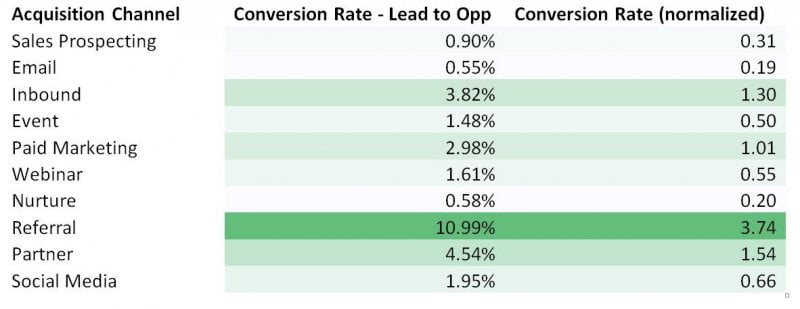
How do I check for stock out in capsim?
Stock outs and their consequences can be diagnosed using the Capstone Courier's Market Share Report (page 10). What is the inventory carrying cost in CapSim? The costs of unsold goods that remain on your shelves are referred to as inventory carry costs.
How to win capsim?
Q 1 How to win Capsim? Make it rain in the earlier rounds by investing heavily in product invention, capacity, and automation, because it takes money to make money. Q 2 How to increase days of working capital in Capsim? The concept is to increase the number of current assets and/or to decrease the number of current liabilities.
What is the inventory carrying cost in capsim?
What is the inventory carrying cost in CapSim? The costs of unsold goods that remain on your shelves are referred to as inventory carry costs. Carrying costs are 2012% of the average unit cost of production for each product line. Is stock out good or bad?
How do you calculate sales forecast for capsim?
Q 13 How do you calculate Capsim sales forecast? Last year’s sales units multiply by the segment growth rate for the upcoming year. Therefore, if you run out of stock in the previous year, adjust the sales unit by adding the additional inventory you would have sold if you didn’t run out of stock.

What causes stock outs in Capsim?
What happens when a product generates high demand but runs out of inventory (stocks out)? The company loses sales as customers turn to its competitors. This can happen in any month.
How do you avoid stock out?
How to reduce stock levels and avoid stock outs.Master your lead times.Automate tasks with inventory management software.Calculate reorder points.Use accurate demand forecasting.Try vendor managed inventory.Implement a Just in Time (JIT) inventory system.Use consignment inventory.Make use of safety stock.More items...
What is stock out cost?
A stockout is when inventory becomes unavailable, preventing an item from being purchased or shipped, resulting in a loss in sales. Stockout costs include the loss of income and customers due to a shortage of inventory from a stockout.
What is the inventory carrying cost in Capsim?
Inventory carry costs are the costs associated with unsold goods that remain on your shelves. For each product line, carrying costs are 12% of the average unit cost of production.
What causes stock out?
A stockout can occur for many reasons: You miscount inventory and end up with less stock than you thought you had. Demand surges for a particular item. Suppliers get delayed.
How can stock availability be improved?
From technology to processes, here are some of the most actionable ways to improve stock availability oversight.Use a reliable inventory management system. ... Implement demand forecasting. ... Use inventory reorder points. ... Distribute your inventory. ... Carry out inventory audits. ... Cultivate healthy supplier relationships.
How is stock out cost calculated?
Raw material requirement per day = 2,070,465 / 300 = 6,902 Kg / days. This following are Stock Out Cost (SOC) calculation: • Raw material requirement (2012) = 2,070,465 Kg / 300 days = 6,901 kg / day • Purchase price difference (if forced to buy if shortage) called as shortage cost = IDR. 250.
How do you calculate stock out?
To calculate the stock out probability, simply divide the number of stock outs by the number of demand requests, then multiply by 100.
What are the techniques of stock out cost determination?
The specific identification method. The First In, First Out (FIFO) method. The Last In, First Out (LIFO) method. The weighted average method.
How do you avoid stock outs in Capsim?
How do you get rid of inventory in Capsim? In the production screen, sell all of the available capacity. Remember that when you liquidate, you must sell all but one unit of capacity in order for the simulation to sell off all inventory at 100 percent of the price.
Is holding cost and carrying cost the same?
Carrying costs, also known as holding costs and inventory carrying costs, are the costs a business pays for holding inventory in stock.
What all factors will lead to reduction of the inventory cost?
Less money tied up in inventory. Less warehouse space is required. Lower insurance costs, as the risk of loss is reduced. Fewer losses due to spoilage, or to expired or out-of-date products.
What does changing a product size and or performance do?
Changing a product size and or performance repositions a product on the perceptual map. In fact, improving a product performance’s and decreasing the size moves the product towards the lower right on the perceptual map.
How to keep on track with SWOT analysis?
In addition, adjust the SWOT analysis at the end of each round to reflect your company’s current positions externally and internally.
How long does it take for a production department to complete an invention?
Production department must purchase production capacity to build the new product one year in advance. Invention projects take at least one year to complete. Example, if one product was invented then capacity would be ordered as follows:
Does Capsim affect stock prices?
Therefore, Capsim emergency loans affect your stock prices even when your company is profitable, plus the interest rate is just ridiculous – it’s 7.5% plus whatever the current debt rate is. In general, once again avoid emergency loans.
What does a region kit do in CapSim?
Region Kits are a feature that allows products to be tailored to the region in which they will be sold. An area's demand for Region Kits is 10% higher than competitively available models, but developers must add or remove the kits 3 months in advance and the materials cost is 15% more.
What does it mean when you stock out in CapSim?
A product that generates high demand also runs out of stock (stocks out). Customers are turning to competitors as a result of the company's sales decline. Every month has the potential to bring this about. Stock outs and their consequences can be diagnosed using the Capstone Courier's Market Share Report (page 10).
What is the inventory carrying cost in CapSim?
The costs of unsold goods that remain on your shelves are referred to as inventory carry costs. Carrying costs are 2012% of the average unit cost of production for each product line.
Is stock out good or bad?
Customers aren't the only ones who are disappointed and frustrated by stockouts. The retailer may also lose sales and revenue and risk damaging its brand if they miss opportunities to engage customers.
What is stock out explain with an example?
The lost revenue and expense associated with a stockout are known as stockout costs. This expense can be incurred in one of two ways: sales-related or non-sales related. In order to obtain inventory, a company may have to pay rush fees and overnight delivery charges.
What are the causes of inventory stock-outs?
Taking an underestimated view of the demand for a given product and, as a result, ordering too little.
How does Capsim calculate contribution margin?
The contribution margin is determined by dividing revenue by labor, costs of materials, and inventory carrying costs. It's described as an average of each company's product portfolio on page 1 of The Courier / FastTrack. At a minimum, 30% would be a good benchmark.
10.3 Excessive Inventory
It is very costly to carry large amounts of inventory (total unit cost is multiplied by a 12% inventory carrying charge). The ideal year-end inventory position is one unit in each product line: one would know that every potential sale was made, and the carry cost would be so small as to be inconsequential.
Typical Problems
Overly Optimistic Sales Forecasts: Previous year customer demands (and segment growth rates) are listed on each market segment analysis. Compare the company's sales forecast figures (found in the Decision Audit, see 3.7.3 Decision Summaries) - against segment demand.
