
To calculate safety stock you must do the following:
- Find the average of a set of data
- Calculate the sum of the average and the data set
- Divide the sum by the sample proportion to get the variance
- Add the variance to the average for the final result
What is safety stock and how do you calculate it?
The calculation of safety stock is – buffer stock formula = (Max Lead Time * Max Sale) – (Average Lead Time * Average Daily Sale) Max Lead Time = As can be seen from the sheet, the maximum lead time taken was in January with 15 days. Max Sale = The month of December had the maximum number of sales.
What is the difference between safety stock and buffer stock?
In order to calculate your safety stock accurately, you’ll need to know the following inputs. Maximum daily usage Maximum daily usage refers to the maximum number of units you expect to sell in a day. This is based on your historical data. Average daily usage Average daily usage refers to the average number of units you sell per day.
How to set safety stock?
Jan 06, 2022 · Although there’s no special formula for fixed safety stock, you can calculate it this way: Fixed safety stock = number of days x average daily usage OR maximum daily usage For example, you can decide to keep two weeks’ worth of safety stock for an item. Its average daily usage is 10 and its maximum daily usage is 17.
How to invest in stocks with a margin of safety?

What is safety stock formula?
Safety stock is calculated by multiplying maximum daily usage (which is the maximum number of units sold in a single day) with the maximum lead time (which is the longest time it has taken the vendor to deliver the stock), then subtracting the product of average daily usage (which is the average number of units sold in ...Feb 5, 2021
What is safety stock with example?
Examples of Safety Stock Suppose a company has a team to research the market demand, and it has estimated that the demand for an umbrella is nearly one thousand units every month. As a precaution, the company can decide to have one hundred units as safety stock because the demand is never constant.Jun 17, 2020
How is safety stock carrying cost calculated?
Inventory carrying cost is a pretty simple calculation once you've figured out all the expenses that go into having these goods on hand. Add all those numbers together for the total carrying costs, then divide it by the total value of the inventory and multiply the result by 100 to get a percentage.Nov 6, 2020
What is the percentage of safety stock?
The higher the desired service level, the more safety stock is required. The retail industry aims to maintain a typical service level of between 90% and 95%, although this does depend on the product being sold. As mentioned before, a higher service level is a risk as it increases the amount of stock being held.Sep 21, 2020
How do you calculate stock?
The most common way to value a stock is to compute the company's price-to-earnings (P/E) ratio. The P/E ratio equals the company's stock price divided by its most recently reported earnings per share (EPS). A low P/E ratio implies that an investor buying the stock is receiving an attractive amount of value.Mar 8, 2022
How do you calculate stock level?
Average Stock Level: The Average stock level is calculated such as: Average Stock Level = Minimum stock Level + 1/2 of Reorder Quantity.
How do you calculate safety stock and reorder point in Excel?
To calculate the reorder point in Excel, set up a table as in the image above, and use the formula =SUM(F2+G2) where Column F is your Safety Stock figure and Column G is your Lead Time Demand.Dec 3, 2020
What is the formula to calculate quantity?
Order Quantity Formula To calculate the optimum order quantity "Q," take the square root of the following: "2N" multiplied by "P" and divided by "H." "N" is the number of units sold per year, "P" is the cost to place one order and "H" is the cost of holding one unit of inventory for one year.Sep 26, 2017
Expert Q&A
Include your email address to get a message when this question is answered.
Tips
There are several other methods to calculate safety stock, but all are based upon using standard deviations to determine demand and lead time variability.
About This Article
This article was co-authored by Michael R. Lewis. Michael R. Lewis is a retired corporate executive, entrepreneur, and investment advisor in Texas. He has over 40 years of experience in business and finance, including as a Vice President for Blue Cross Blue Shield of Texas.
What is the basic safety stock formula?
The basic safety stock formula is the traditional method and takes into account the number of products you sell per day and the number of days of stock you want to hold at any one time.
What is the final element to consider before we get into calculating safety stock?
The final element to consider before we get into calculating safety stock using the safety stock formula is the reorder point calculation. This is relatively simple to understand and a really useful calculation to know.
Why is safety stock management important?
Safety stock management is a critical part of being a retailer and a manufacturer. It will help to reduce the chance of stock outs, which lead to inefficiency, unhappy customers, and ultimately, lost sales and reduced profits.
What are the challenges of modern retail?
One of the biggest challenges in modern retail and manufacturing is stock management. New trends, fluctuating demands and a constantly changing retail landscape all impact which products should be stocked and how many of each must be on the shelves and in the warehouse to maximize efficiency and reduce costs.
How does running out of stock affect your business?
Some of the direct impacts on your business include: Loss of revenue. Loss of gross profit.
When dealing with uncertainties and multiple variables, the best way to calculate safety stock is to use standard deviation to determine variations in
When dealing with uncertainties and multiple variables, the best way to calculate safety stock is to use standard deviation to determine variations in supply and demand. The definition of standard deviation is a quantity calculated to indicate the extent of deviation for a group as a whole.
What is safety stock?
Safety stock is simply extra inventory held by a retailer or a manufacturer in case demand increases unexpectedly. This means it’s additional stock above the desired inventory level that you would usually hold for day-to-day operations.
What is safety stock?
Safety Stock is defined as the additional quantities of goods stored as a safety net above the required amount to prevent going out of stock due to emergencies. An example of emergency is when sold off goods undergo damage on their way to be delivered. In such a case, safety stock can be used to ensure that the customer receives ...
How to calculate lead time?
#1 – Average – Max Method 1 Max sales = the day with the highest number of items sold. 2 Average sales = average daily sales 3 Lead time = in this contest, the lead time is the time period from the point a business places an order to restock its supplies until the supplier actually delivers them. 4 The lead time is calculated in terms of days. 5 Max lead time = the maximum number of days taken by the supplier to deliver the stock since placing its order.
Safety stock formula inputs
In order to calculate your safety stock accurately, you’ll need to know the following inputs.
Take the guessing out of inventory management & fulfillment with ShipBob
Connect your store, import your products, then send us your inventory.
Distributed inventory
With ShipBob’s network of fulfillment centers, you can strategically split your inventory across our locations to get your products from point A to point B more quickly and affordably. Storing inventory near your customers helps reduce the shipping zones and costs associated with shipping orders to faraway destinations.
Order management
At ShipBob, we track your orders from A to Z. Filter orders by status, search for specific orders, see a quick timeline view of where your order is in the fulfillment process (e.g.
Reporting and analytics
To provide you with visibility into our operations and performance, and also hold ourselves accountable, ShipBob’s free analytics tool is packed with charts to help you with everything from year-end reporting, to better supply chain decision-making.
End-to-end customer experience
We care about the customer experience as much as you and strive to be an extension of your team. From custom branded boxes to free plain packaging, ShipBob works with you to provide the unboxing experience you want. We also help you offer the fastest, most cost-effective shipping options to meet your customers’ expectations.
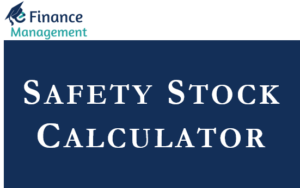