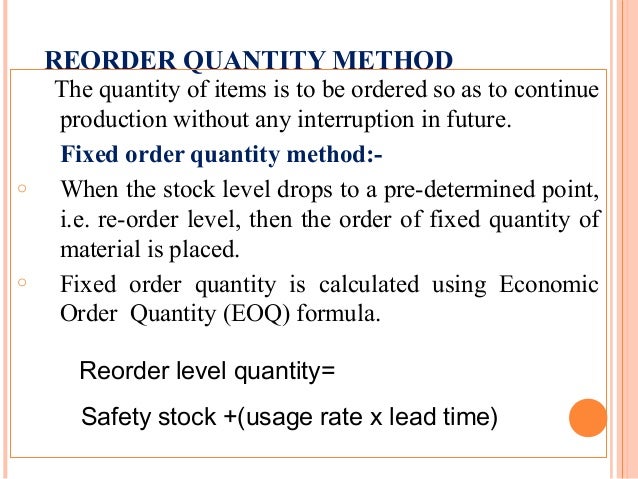
Step by Step Reorder Point Calculation
- Calculating Daily Usage and Lead Time. Firstly, we need data for our calculations. ...
- Let’s look at an example using the lead time demand formula. Clara is the manager of a home appliance store. ...
- Safety Stock. ...
- Reorder Point = 8 units (Lead time demand) + 41 units (Safety Stock) = 49 units. ...
What is safety stock and re-order point?
Nov 30, 2020 · To estimate the number we’ll use during this time, we multiple the average daily demand by the average lead time. How to Calculate Lead Time Demand How to Calculate Reorder Point Adding our safety stock level to the lead-time demand gives us our reorder point. But what does the reorder point tell us to do?
How to find safety stock?
Mar 13, 2021 · It’s easy to calculate the reorder point once you have the safety stock level. The reorder point tells you the stock level at which the new order should be triggered (which assumes it’s instantaneous). It is calculated by adding the safety stock metric to the sum of the lead time multiplied by the average units sold daily.
How to calculate safety stock?
Sandy’s Reorder Point = (20 X 5) + safety stock = 100 + safety stock In order to complete the formula, we’ll need to figure out Sandy’s safety stock. How to Calculate Your Safety Stock “Safety stock” is your emergency stock — a buffer amount of inventory meant to carry you through fluctuations in demand.
How to calculate the reorder point?
Oct 24, 2019 · 5 Reorder Point Planning Strategies. 1. Avoid Using Absolute Reorder Point. It might be tempting to set reorder points then move on to the next vital project, but things change. Demand ... 2. Automate Your Reordering Process with Technology. 3. Lean into Product Performance. 4. Build A Strong Supply ...
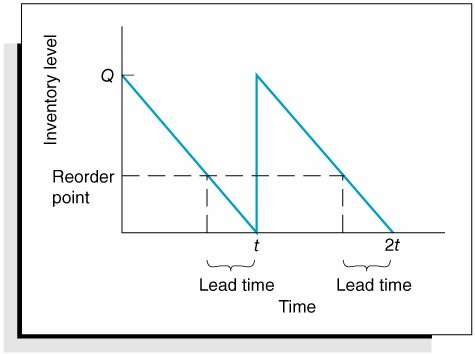
What is the formula of reorder point?
The basic formula for the reorder point is to multiply the average daily usage rate for an inventory item by the lead time in days to replenish it.Jan 19, 2022
Is safety stock included in the reorder level?
How does safety stock affect reorder point?
Is safety stock the same as reorder point?
How do you calculate replenishment order quantity?
...
Let's look at an example of how to calculate reorder quantity for an individual product:
- ADU = 10 units.
- ALT = 29 days.
- Your reorder quantity is equal to 290.
How do you calculate reorder level and reorder level?
What is the safety stock formula?
How do you calculate safety stock and reorder point in Excel?
How do you calculate normal reorder period?
How do you know when to order inventory?
What is the reorder point?
The reorder point is a metric used by businesses that handle inventory to determine the minimum quantity of items that they should have available i...
How do you calculate reorder point?
In order to calculate reorder point, a business has to know the average unit sales per day, the average lead time and the amount of safety stock th...
Why is reorder point important?
Knowing the reorder point per item is key for efficient inventory management. It optimizes holding costs, prevents stockouts, avoids overstocking,...
What is safety stock?
In basic terms, safety stock is the amount of extra stock that is maintained by a business to reduce the risk of stockouts caused by supply and dem...
The Zero Safety Stock Model
The zero safety stock model is a very risky way to plan inventory since variations in demand and supplier delivery times happen every day and this makes our calculations merely estimates.
How to Calculate Safety Stock
Inventory planners keep safety stock to deal with this reality. Safety stock is a buffer of inventory to help deal with sources of variation. I’ve mentioned two of those sources already: variation in delivery lead times from your supplier and variations in the daily or weekly demand for this inventory item.
Sample Calculation
Let’s put some numbers in our equation to see how this works. Suppose we have a supplier that has been delivering this item to us, on average, in 14 days. However, over the last year, there have been deliveries of this item that have taken as much as 25 days to reach us.
How to Calculate Reorder Point
Adding our safety stock level to the lead-time demand gives us our reorder point.
Order Quantity
Using this method, how much do you order? I have said that the company likes to order 13 weeks of inventory. This order amount works in the case where you haven’t had to use any of your 4-week buffer to deal with sources of variation. However, suppose this company finds that it had to use 3 weeks of its 4-week buffer to deal with a surprise order.
Summary
Reorder points and safety stock levels are useful calculations to better manage your inventory, but sometimes access to the right data may force you to use an approximation for some of the values. Most companies can easily obtain daily or weekly sales data. It’s the variation in the supplier delivery times that is more difficult to obtain.
How to determine reorder point?
In order to figure out your reorder point, you’ll need a couple of pieces of information: 1 Average daily unit sales: How many units do you sell per day, on average? 2 Lead time: How long does it take for an order to arrive from your supplier?
Is a reorder point static?
Your reorder point is not static. It is different for every product, and might even vary with the season. Depending on your business, keeping track of your own inventory and calculating these dynamic safety stock and reorder points manually ranges from time-consuming to practically impossible. Even if you run an ecommerce shop and you track inventory digitally, managing reorders still takes a significant amount of time. You’ll need to put in the work to account for every item sold.
What is inventory management software?
Inventory management software is an easy solution. Business can change on a dime, so being able to view and adjust your inventory anywhere is an advantage. This is especially true if you’ve got multiple locations or employees who need to access your inventory data out of office.
How long does it take for a supplier to deliver an order?
Supplier A takes five business days to deliver an order, Supplier B takes seven days. For Supplier B, your reorder point will be higher because you need to account for more days of stock between your order and when new stock arrives.
What happens if you understock?
Understocking can have devastating consequences for retailers, and can leads to: 1 Inability to make sales, due to scarce or non-existent inventory 2 Declining customer service, with your consumer base moving on to competitors with more reliable and consistent inventory 3 Higher vendor costs for rushed purchase orders if you need to replenish stock 4 Negative impact on your company's overall image and any consumer ratings
How to calculate reorder point?
First, calculate your daily sales (a 30-day or weekly average is fine). Then multiply it by the number of days it takes between ordering a product from your supplier and receiving it. Then, calculate your safety stock and add both numbers. The result will be your official reorder point.
What is reorder point?
Reorder point refers to that stage of inventory management in which the inventory needs to be reordered to ensure timely availability of goods for the sales. It ensures that a business can have a minimum product quantity in storage to prevent operational disruptions arising out of a stockout. At the same time, reorder point will prevent holding ...
Why is reorder point important?
At the same time, reorder point will prevent holding stock beyond the safety point to avoid incurring unnecessary storage costs.
Why is it important to avoid overstocking?
It is also essential to avoid overstocking because it will increase your inventory holding costs and diminish overall profits. To calculate the reorder point, you need to know your daily sales, lead times, and safety stock levels.
What is raw materials inventory?
Raw Materials Raw materials inventory is the cost of products in the inventory of the company which has not been used for finished products and work in progress inventory.
What is reorder point?
To understand how to put together a reorder point planning strategy, let’s identify some key concepts that factor into the process.
What is safety stock?
Another concept that is crucial to a reorder point planning strategy is safety stock .
Understanding the reorder point formula
The reorder point formula is used to calculate your reorder point accurately instead of guessing or waiting until stock runs out.
Strategies for reorder point planning
Building a reorder point planning strategy doesn’t have to be overwhelming.
How to reorder points?
You then multiply this by the number of days of stock you want to carry. This is usually related to lead time, to ensure your ordering point is set at a level where there is enough stock to last until your next delivery:
Is safety stock a buffer?
You may be thinking that safety stock will act as the buffer against any fluctuations in demand or lead times. And this is true for items where demand and lead times are consistent and predictable, but not when they are more erratic.
Can you use historical average consumption to calculate lead time forecasts?
Using historic average consumption to calculate lead time forecasts works well if you sell the same amount of each item in every period. But if sales fluctuate over a couple of periods, then you’re going to suffer with either stockouts, or excess inventory.
Is lead time reliable?
In addition, many lead times are not as reliable or regular as they used to be. Using a ‘one size fits all’ reorder point and safety stock formula to calculate replenishment needs will, therefore, lead to stock availability challenges.
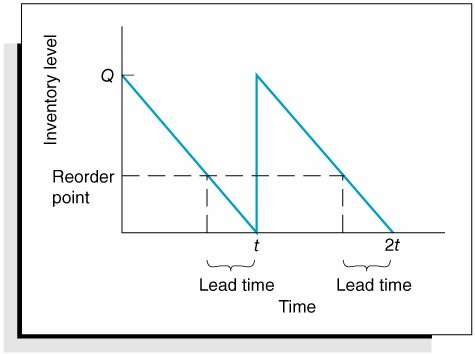