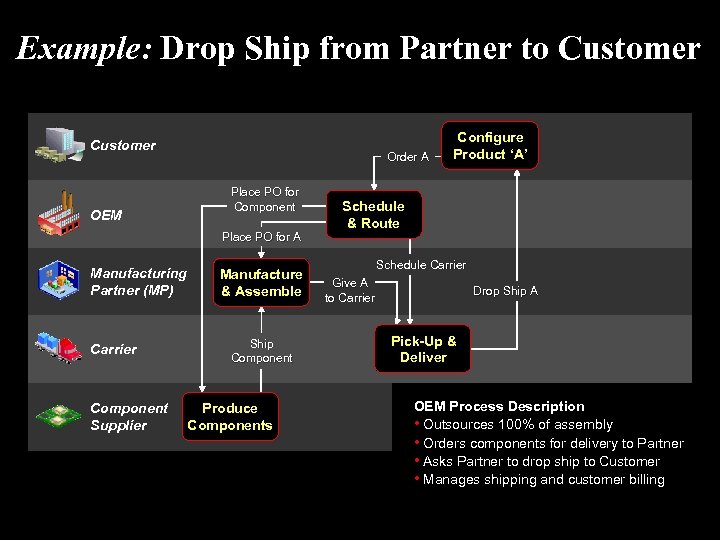
How much safety stock do you need?
The higher the desired service level, the more safety stock is required. The retail industry aims to maintain a typical service level of between 90% and 95%, although this does depend on the product being sold.
How to calculate safety stock from forecast error?
When a company is involved in forecasting, one can calculate the error ei = xi – fi, where xi, fi, and ei represent the actuals, forecast, and the error respectively for period i. The recommended formula for variance then becomes: When one uses the second formula, the safety stock is calculated from the variance of the forecast error.
Does safety stock apply to actual demand?
Regarding actual demand, safety stock applies only to common-cause variation. Please follow my line of reasoning, and I so appreciate your interest, attention and participation in a discussion! First, three definitions: 1. Safety stock, or SS: Not just the MRP-specific adder to gross requirements, but the general concept of buffer inventory.
How much safety stock is required to cover demand variability?
The general equation for the amount of safety stock required to cover demand variability is: Z is the Z factor and is demand variability. Figure 2 shows the relationship between Z and service level.

What amount of safety stock is appropriate?
Typical safety stock policies include: Safety stock is equal to a fixed percentage of lead time usage (typical value is 50% of lead time usage) or. A specific number of day's supply is maintained as safety stock (typical value is seven to 14 days)
When should safety stock be increased?
As shown in the graph, safety stock increases with the customer service level. When the service level values reach above 95% the safety stock number increase exponentially. Statistically speaking, the safety stock is infinite for a 100% service level. The safety stock equation is designed to deal with variability.
How do you calculate optimal stock level?
To calculate the stock level, simply add together the optimal order quantity, minimum stock amount, and safety stock amount.
How do firms decide on the required level of safety stock in chain?
Applying the 50% rule of safety stock To help you get started on determining your safety stock levels, the 50% rule is a generally accepted starting point that businesses use. To continue our example, the vendor's delivery time averages 10 business days and Company A's daily sales average 20 units.
What does a 95% service level mean?
So, a 95% service level means that there's only a 5% likelihood of stocking-out. However, when someone refers to service level they might be referring to Fill Rate – the percentage of demand that was satisfied without regard to the probability of stock out.
What is safety stock formula?
Average – Max Safety Stock Formula It calculates the average maximum number of units that are needed at any given time. (Maximum amount of sales x Maximum lead time) – (Average amount of sales x Average lead time)
What is ideal stock level?
In logistics, optimal stock designates the exact amount of inventory a business requires to fulfill routine demand without the occurrence of a stockout. In other words, it involves obtaining maximum profitability and bringing storage costs down to a minimum.
How do you predict inventory needs?
Essential data elements required for accurate inventory forecasting include the following:Current inventory levels.Outstanding purchase orders.Historical trendlines.Forecasting period requirements.Expected demand and seasonality.Maximum possible stock levels.Sales trends and velocity.More items...•
What's a good inventory turnover ratio?
between 5 and 10For most industries, the ideal inventory turnover ratio will be between 5 and 10, meaning the company will sell and restock inventory roughly every one to two months. For industries with perishable goods, such as florists and grocers, the ideal ratio will be higher to prevent inventory losses to spoilage.
What is minimum level and safety stock?
Minimum Stock Level: Definition and Explanation In other words, a minimum stock level is a minimum quantity of a particular item of material that must be kept at all times. The fixing of this level acts as a safety measure. For this reason, the minimum stock level is commonly known as safety stock or buffer stock.
What is danger stock level?
Danger level is that level below which the stock should under no circumstances be allowed to fall. Inventory Management- Concept, Benefits and costs of holding inventories, Inventory Control Techniques- ABC Analysis, EOQ, Reorder level, Maximum and Minimum Level, Danger level, Safety stock.
What is the formula of minimum stock level?
(vi) Average Stock level = (Maximum stock level + Minimum stock level) x 14 or Minimum Stock level + 14 Reorder Quantity. Obviously, the Reordering level is below the Maximum level, and Minimum level is below the Reordering level and the Danger level is below the Minimum level. Safety Stock is above minimum level.
What is safety stock?
Safety stock is a category used by retailers and logistics specialists to specify a level of extra stock that the business should keep to make sure...
How to calculate safety stock?
The two basic options to define safety stock are considered. The first one implies calculations based on historical distribution while the second o...
What are the main distribution models?
To estimate uncertainty in demand planning, retailers use distribution models divided into three major types: uniform, triangular, and normal one.
How can software help in safety stock management?
Most often, retailers use advanced software to predict the demand, find the optimal safety stock or set prices so they can hit the targeted stock l...
Why do we need safety stock?
Although we know the consequences of not having enough stock, why do you need safety stock in the first place? The reason for having a safety stock strategy is to protect you against two external factors over which you have little to no control: demand uncertainty and lead time uncertainty.
Why is safety stock lower?
If your lead time variation is small, you will likely have a much lower safety stock because you know your supply will be fairly consistent. On the other hand, if your supply fluctuates dramatically you will require more safety stock to cover these longer lead time periods.
What causes stockouts?
Stockouts are usually caused by: Changes in consumer demand. Incorrect stock forecasts. Variability in lead times for raw materials. Trying to plan for these variables and maintain a target inventory level can be difficult. However, this is where a safety stock formula comes in.
How does running out of stock affect your business?
Some of the direct impacts on your business include: Loss of revenue. Loss of gross profit.
Why is lead time important?
For manufacturers and companies that assemble products using different components, lead time is a critical factor to determine minimum inventory and safety stock requirements.
Why do retailers use safety stock?
One of the main reasons that retailers and manufacturers implement a safety stock strategy is to prevent stockouts. Stockouts are usually caused by: Changes in consumer demand.
When dealing with uncertainties and multiple variables, the best way to calculate safety stock is to use standard deviation to determine variations in?
When dealing with uncertainties and multiple variables, the best way to calculate safety stock is to use standard deviation to determine variations in supply and demand. The definition of standard deviation is a quantity calculated to indicate the extent of deviation for a group as a whole.
How accurate are safety stock calculations?
While the safety stock calculations become more complicated, they are also much more accurate as they take into account target service levels, forecast accuracy/error and lead time variability.
What is a fixed level of safety stock?
Many companies set a fixed level of safety stock for their inventory items – that is, they add a ‘best-guess’ quantity to the reorder point to allow for any issues.
How many units of safety stock are left in Showerhead A?
Showerhead A sees actual sales that are higher than the forecast, but the safety stock does its job by providing enough stock to cover the rise in demand with 295 units of safety stock remaining.
What is safety stock?
Safety stock is defined as inventory that is carried to prevent stock outs and back order situations. Stock outs stem from factors such as fluctuating customer demand, forecast inaccuracy, and variability in supplier lead times. Many companies look at their own demand fluctuations and assume that there is not enough consistency to predict future ...
What happens if you don't carry enough stock?
If you carry too much inventory, you risk tying-up much needed working capital. But if you don’t carry enough, you face stock-outs and reduced service levels. An important piece of this puzzle is to accurately calculate safety stock levels.
What is the purpose of safety stock?
The purpose of safety stock is to minimize disruption to order fulfilment while investing the lowest possible amount of capital in inventory.
How to contact Eazystock?
To understand more about how EazyStock inventory optimization software can help ensure you have accurate safety stock levels, contact us today on +1 (844) 416-5000 or request a demo:
Why is safety stock important?
However, the importance of safety stock is crucial across all the retail industries from grocery, consumer electronics or DIY to footwear and apparel with their dependancy on seasonality. In each case, relevant predictions remain and will always be one of the crucial prerequisites of a retailer’s success. This article will shed light on how to calculate safety stock and align it with optimal service level based on correct distribution forecasts and what has advanced software to do with it.
What is safety stock?
Safety stock is a key category when it comes to retail forecasts, distribution, and service level. Discover fundamental models underlying long-term predictions in retail and find why pricing software is inevitable.
Why do retailers keep safety stock?
To deal with this kind of issues, retailers keep safety stock as an extra inventory minimizing the risk of stock out or other negative events.
Why is inventory planning important?
Distribution models are, in turn, essential in inventory planning as they help retailers to find how many items of each product should be in stock. To estimate uncertainty in demand planning, retailers use distribution models divided into three main types: uniform, triangular, and normal one.
What is safety factor in a model?
‘Safety factor’ in the model marks a number of standard deviations corresponding to a specific service level.
What is service level?
Most often, service level is defined as a probability of not hitting a stock-out or the probability of not losing sales. The definition shows that level of stocks is one of the most important aspects while considering service level.
What is the most common way to calculate service level?
The correlation between the quantity of delivered products and demanded ones is the most common way to calculate service level. However, depending on industry, market segment or retail type, the other criteria could also be applied. The table below shows the most common ones.
How to find the safety stock formula?
The last step is to use the safety stock formula: Safety stock = Z x ∑LT x D
Why is safety stock important?
Calculating safety stock through a formula is important because it can allow companies to make more accurate estimations regarding how much extra inventory they need to purchase to meet sudden demand increases. By using a safety stock formula, you can minimize the risk of losing customers or profits by spending just the right amount on extra inventory or manufacturing.
How to calculate standard deviation?
First, they add the data set together (3 + -1 + 1 + 4 = 7) and then divide that number by the amount of values in the data set (7/4), making the average time variance 1.75. Then, they add the average difference to the estimated restock time of 7 days, which equals 8.75 days, the standard deviation.
What is safety stock?
Safety stock is a certain amount of extra inventory that stores and manufacturers hold in case customer demand suddenly increases. Safety stock gives companies the ability to meet customer demands while countering the risks of losing profits.
Why do companies only want to provide a 75% service level?
If a company only wants to provide a 75% service level, they might do that to save money on purchasing extra safety stock inventory. However, they also increase their risk of unsatisfied customers if their inventory were to run out.
What is lead time in stock?
Lead time refers to the amount of time it takes to complete a task from start to finish. For a company trying to calculate safety stock, the lead time often refers to how long it takes for inventory to be ordered and restocked from the time a store or manufacturer runs out.
What is standard deviation?
Standard deviation is a calculation that allows you to find an accurate estimated range within a certain set of data. Use these three steps to calculate standard deviation:
What is scenario 2 of DFE?
Scenario 2 – DFE from forecast bias (uniform, see above): -When mean forecast demand is chronically and consistently above or below mean actual demand. Its cause? Perhaps over- or under-optimism, unmaintained planning BOMs and other culprits. Bias is not common-cause demand variation and has no place in determining SS.
What is forecast bias?
Forecast bias (uniform): Chronic, ongoing multi-period bias with a uniform, same-direction difference between actual-demand and forecast-value averages for those periods. In this scenario, we will not include common-cause variation.
How long has David been in lean and flow?
David has over 30 years of experience in lean and flow, MRP, information technology, cost accounting and finance across a broad range of industries. Since 1994, he has implemented lean and flow worldwide in scores of facilities and industries, including regulated environments.
Does forecast to actual demand variation affect safety stock?
Here is my theme: Forecast-to-actual demand variation has no place in determining safety stock (or buffer inventory of any form). Regarding actual demand, safety stock applies only to common-cause variation. Please follow my line of reasoning, and I so appreciate your interest, attention and participation in a discussion!
Is 98% SL achievable?
Note – 98% SL is achievable, but only by employing negative SS (possible with ROP, but not with MRP). Chronic positive bias alone provides more than enough de facto SS, even when formal incremental SS = 0. DFE-based SS drives inventory even higher, achieving an undesired 100% SL and AQOH that’s at least 1.5 times higher than optimal.
Does SS apply to actual demand?
Since SS applies only to common-cause variation in historical actual demand, why not simply analyze this actual demand, avoiding the extra effort, and risks of diluting common-cause variation, inherent in determining and using DFE?
Can supply chain professionals check inventory for bias?
In practice, a supply-chain professional may not be able to check all of his or her inventory items for forecast bias. Yet bias distorts common-cause demand variation needed for DFE-based SS. Only historical actual demand data, not DFE, is meaningful for correct SS.
Why do companies need safety stock?
In such a case, safety stock can be used to ensure that the customer receives the product regardless of the emergency. Companies bear additional costs of maintaining the extra stock to serve their customers well.
What is safety stock?
Safety Stock is defined as the additional quantities of goods stored as a safety net above the required amount to prevent going out of stock due to emergencies. An example of emergency is when sold off goods undergo damage on their way to be delivered. In such a case, safety stock can be used to ensure that the customer receives ...
Why are there uncertainties in the stock market?
Uncertainties could be anything, such as a sudden hike in demand. Not having extra stock will lead a business to lose on an opportunity. For instance, newly launched iPhones and PlayStations become out of stock because of low supply and high demand. Accidents, delays, floods, cyclones, landslides, or heavy snowfall directly impact the supply lines.
Why do we need buffer stock?
Buffer stock protects us from inconsistency in demand and lead time or inaccurate forecasting. It helps us in the continuous flow of business.
How to calculate lead time?
#1 – Average – Max Method 1 Max sales = the day with the highest number of items sold. 2 Average sales = average daily sales 3 Lead time = in this contest, the lead time is the time period from the point a business places an order to restock its supplies until the supplier actually delivers them. 4 The lead time is calculated in terms of days. 5 Max lead time = the maximum number of days taken by the supplier to deliver the stock since placing its order.
What happens if a bakery has buffer stock?
If the bakery has maintained a buffer stock, it will manage for a day or two without disappointing its customers till its pantry gets restocked. Although we may not fully prepare for such a scenario, we can certainly try to mitigate the effects, which can be done by maintaining a buffer stock.
What is holding costs?
Maintaining stocks already involves ordering costs, holding costs Holding Costs Holding cost refers to the cost that an entity incurs for handling and storing its unsold inventory during an accounting period. It is calculated as the sum total of storage cost, finance cost, insurance, and taxes as well as obsolescence and shrinkage cost. read more, and spoilage costs. Adding any buffer stock will further overburden a company.
What is safety stock?
Safety stock is there to protect you from late or part deliveries and from underestimating your sales. There are a few factors and considerations to take into account when calculating what your safety stock should be.
What factors do insurance companies look at when determining your risk level?
Factors that insurance companies look at when determining your risk level are things like age, sex, demographics, and previous history. The same considerations apply when looking at your safety stock. Insurance companies look at the history and behavior of the driver; inventory planners look at the history and behavior of a stock item ...
Can you set safety stock in units?
Some inventory management systems and tools allow you to set the safety stock or minimum stock in units. If you are using units, for example, 100 units in high season may not be enough, but in the low season may be way too much. Rather use a time metric.
About the Author: Sujit Singh
As COO of Arkieva, Sujit manages the day-to-day operations at Arkieva such as software implementations and customer relationships. He is a recognized subject matter expert in forecasting, S&OP, and inventory optimization. Sujit received a Bachelor of Technology degree in Civil Engineering from the Indian Institute of Technology, Kanpur, and an M.S.
About the Author: Manjeeth Vijayan
Manjeeth A Vijayan is a Senior Consultant at Arkieva, India. He is responsible for analyzing client’s supply chain processes, configuring and implementing Arkieva software, thereby, helping clients improve efficiencies in their supply chain planning.
